En Construcción.
Metrología y Uso de Instrumentos de Medición: Precisión y Exactitud en el Montaje de Estructuras Metálicas
La metrología, la ciencia de la medición, es fundamental en el montaje de estructuras metálicas. La precisión y la exactitud en las mediciones son esenciales para garantizar la calidad, la seguridad y la funcionalidad de la estructura. Un error de medición, por pequeño que sea, puede tener consecuencias graves, como el desalineamiento de los elementos estructurales, la inestabilidad de la estructura, el incumplimiento de las especificaciones técnicas y, en última instancia, el colapso de la estructura.
En el montaje de estructuras metálicas, se utilizan diversos instrumentos de medición para verificar las dimensiones, la alineación, la nivelación, la plomada y otros parámetros de los elementos estructurales. Es fundamental que los trabajadores que realizan estas mediciones estén debidamente capacitados en el uso correcto de los instrumentos, en la interpretación de los resultados y en el registro de las mediciones.
En Colombia, y en ciudades como Bogotá, donde la construcción de edificaciones e infraestructuras debe cumplir con rigurosas normas de sismo resistencia (NSR-10), la metrología y el uso adecuado de instrumentos de medición son aún más importantes. Las empresas constructoras deben asegurar que sus trabajadores cuenten con la capacitación y las herramientas necesarias para realizar mediciones precisas y confiables.
Conceptos de Precisión y Exactitud: Entendiendo la Diferencia
En metrología, es importante distinguir entre precisión y exactitud, ya que son conceptos diferentes que a menudo se confunden:
- Precisión: Se refiere a la repetibilidad o reproducibilidad de una medición. Un instrumento de medición es preciso si, al medir varias veces la misma magnitud, se obtienen valores muy cercanos entre sí, es decir, con poca dispersión. La precisión indica la calidad del instrumento y la habilidad del operador para realizar mediciones consistentes.
- Exactitud: Se refiere a la cercanía de una medición al valor verdadero de la magnitud medida. Un instrumento de medición es exacto si el valor medido se acerca al valor real. La exactitud indica qué tan bien se ajusta la medición a la realidad.
Es posible tener un instrumento muy preciso pero poco exacto, o viceversa. Por ejemplo:
- Un instrumento puede ser muy preciso (siempre da el mismo resultado al medir lo mismo), pero inexacto (si ese resultado está sistemáticamente alejado del valor verdadero). Esto podría deberse a un error de calibración del instrumento.
- Un instrumento puede ser exacto en promedio (la media de varias mediciones se acerca al valor verdadero), pero impreciso (las mediciones individuales varían mucho entre sí). Esto podría deberse a un error aleatorio en la medición.
El objetivo ideal es tener instrumentos de medición que sean tanto precisos como exactos. Para lograr esto, es fundamental:
- Utilizar instrumentos de medición de buena calidad y adecuados para la tarea.
- Calibrar los instrumentos periódicamente.
- Capacitar a los trabajadores en el uso correcto de los instrumentos y en la interpretación de los resultados.
- Realizar varias mediciones de la misma magnitud y calcular el promedio.
- Controlar los factores que pueden afectar la precisión y la exactitud de las mediciones (p. ej., temperatura, humedad, vibraciones).
Calibración de Instrumentos: Asegurando la Confiabilidad de las Mediciones
La calibración de un instrumento de medición es el proceso de comparar sus mediciones con un patrón de referencia conocido y, si es necesario, ajustarlo para que sus mediciones sean lo más precisas y exactas posible. La calibración es fundamental para garantizar la confiabilidad de las mediciones y para asegurar que los instrumentos cumplan con los requisitos de calidad y las normas técnicas.
La calibración debe realizarse:
- Periódicamente: La frecuencia de calibración depende del tipo de instrumento, su uso y las recomendaciones del fabricante. Algunos instrumentos deben calibrarse cada año, otros cada seis meses, y otros incluso con mayor frecuencia.
- Después de un Golpe o Caída: Si un instrumento ha sufrido un golpe, una caída o cualquier otro evento que pueda haber afectado su precisión, debe ser calibrado antes de volver a utilizarse.
- Antes de un Trabajo Crítico: Si se va a utilizar un instrumento para realizar una medición crítica, es recomendable calibrarlo antes de realizar la medición.
- Cuando se Sospeche de un Error: Si se sospecha que un instrumento está midiendo incorrectamente, se debe calibrar para verificar su precisión.
La calibración debe ser realizada por personal capacitado y utilizando patrones de referencia trazables a patrones nacionales o internacionales. Los patrones de referencia son instrumentos o materiales de medición de alta precisión que se utilizan para calibrar otros instrumentos.
Después de la calibración, se debe emitir un certificado de calibración que indique:
- La identificación del instrumento calibrado.
- La fecha de calibración.
- Los resultados de la calibración (las mediciones obtenidas antes y después del ajuste, si lo hubo).
- La incertidumbre de la medición.
- Los patrones de referencia utilizados.
- El nombre y la firma de la persona que realizó la calibración.
- La fecha de la próxima calibración.
Es importante que las empresas mantengan un registro de la calibración de todos sus instrumentos de medición y que se aseguren de que los instrumentos se calibren periódicamente según lo establecido. El uso de instrumentos no calibrados puede generar errores en las mediciones, lo que puede tener consecuencias graves en el montaje de estructuras metálicas.
En Colombia, existen laboratorios acreditados por el Organismo Nacional de Acreditación de Colombia (ONAC) que ofrecen servicios de calibración de instrumentos de medición.
Manejo de Instrumentos de Medición (Niveles, Teodolitos, Estaciones Totales): Técnicas y Precauciones
En el montaje de estructuras metálicas se utilizan diversos instrumentos de medición para verificar la alineación, la nivelación, la plomada, los ángulos y las distancias de los elementos estructurales. Algunos de los instrumentos más comunes son:
- Niveles: Se utilizan para verificar la horizontalidad o verticalidad de una superficie o un elemento estructural. Existen diferentes tipos de niveles, como:
- Nivel de Burbuja: Es el nivel más común. Consiste en un tubo lleno de líquido con una burbuja de aire. Cuando la burbuja está centrada, la superficie está nivelada.
- Nivel de Manguera: Se utiliza para nivelar puntos distantes. Consiste en una manguera transparente llena de agua. El nivel del agua en ambos extremos de la manguera indica si los puntos están nivelados.
- Nivel Láser: Proyecta un rayo láser que indica una línea o un plano horizontal o vertical. Es muy preciso y se utiliza para nivelar grandes superficies o para trabajos de alta precisión.
- Nivel Digital: Muestra la inclinación de una superficie en una pantalla digital.
- Verificar que el nivel esté limpio y en buen estado antes de usarlo.
- Colocar el nivel sobre una superficie estable y plana.
- Asegurarse de que la burbuja esté centrada (en el caso del nivel de burbuja) o de que la lectura sea cero (en el caso del nivel digital).
- Proteger el nivel de golpes, caídas y temperaturas extremas.
- Calibrar el nivel periódicamente.
- Teodolitos: Se utilizan para medir ángulos horizontales y verticales con alta precisión. Los teodolitos son instrumentos ópticos que constan de un telescopio montado sobre una base giratoria.
- Teodolito Óptico: El operador lee los ángulos en escalas graduadas a través del telescopio.
- Teodolito Electrónico: Muestra los ángulos en una pantalla digital.
- Trípode estable: Asegurarse de que el trípode esté firmemente plantado en el suelo y nivelado.
- Nivelación del teodolito: Utilizar los tornillos nivelantes para centrar la burbuja del nivel esférico y del nivel tubular.
- Puesta en estación: Colocar el teodolito sobre un punto de referencia conocido (estación) y orientarlo hacia otro punto de referencia conocido.
- Lectura de ángulos: Aprender a leer correctamente las escalas graduadas (en el caso de teodolitos ópticos) o interpretar las lecturas digitales (en el caso de teodolitos electrónicos).
- Evitar vibraciones: No tocar el teodolito ni el trípode durante la medición.
- Protección: Proteger el teodolito de golpes, caídas, polvo, humedad y temperaturas extremas.
- Calibración: Calibrar el teodolito periódicamente.
- Estaciones Totales: Son instrumentos electrónicos que combinan las funciones de un teodolito y un distanciómetro. Permiten medir ángulos horizontales y verticales, distancias y coordenadas con alta precisión. Las estaciones totales son muy utilizadas en topografía y construcción para realizar levantamientos, replanteos y control de obras.
- Estación Total Robótica: Puede ser controlada a distancia y realizar mediciones de forma automática.
- Trípode y nivelación: Similar al teodolito.
- Puesta en estación y orientación: Similar al teodolito, pero se utilizan prismas reflectantes como puntos de referencia.
- Configuración: Configurar la estación total con los parámetros correctos (unidades de medida, correcciones atmosféricas, constantes del prisma, etc.).
- Medición: Aprender a utilizar las funciones de medición de la estación total (medición de ángulos, distancias, coordenadas, replanteo, etc.).
- Baterías: Asegurarse de que las baterías estén cargadas antes de usar la estación total.
- Protección: Proteger la estación total de golpes, caídas, polvo, humedad y temperaturas extremas.
- Calibración: Calibrar la estación total periódicamente.
- Manejo de datos: Aprender a descargar y procesar los datos medidos por la estación total utilizando software especializado.
El manejo de teodolitos y estaciones totales requiere capacitación específica y práctica. Es fundamental que los trabajadores que utilizan estos instrumentos conozcan su funcionamiento, sus limitaciones y las precauciones que deben tomar para obtener mediciones precisas y confiables.
Las empresas deben proporcionar a sus trabajadores la capacitación necesaria y deben asegurarse de que se utilicen los procedimientos correctos para el manejo de estos instrumentos.
Uso de Flexómetros y Cintas Métricas: Midiendo Longitudes con Precisión
Los flexómetros (cintas métricas retráctiles) y las cintas métricas son herramientas básicas pero esenciales en el montaje de estructuras metálicas. Se utilizan para medir longitudes, anchos, alturas y profundidades de los elementos estructurales, verificar dimensiones, controlar la alineación y el espaciamiento, y realizar replanteos.
Aunque su uso parece sencillo, es importante seguir algunas recomendaciones para obtener mediciones precisas y evitar errores:
- Selección Adecuada:
- Utilizar un flexómetro o cinta métrica de la longitud adecuada para la medición. No intentar medir distancias mayores a la longitud de la cinta.
- Utilizar un flexómetro o cinta métrica con la graduación adecuada (milímetros, centímetros, pulgadas).
- Utilizar un flexómetro o cinta métrica de un material resistente y duradero (acero, fibra de vidrio).
- Inspección Previa:
- Verificar que el flexómetro o cinta métrica esté en buen estado, sin dobleces, roturas, óxido o desgaste excesivo.
- Verificar que el gancho o uña del extremo esté firme y no tenga juego.
- Verificar que el mecanismo de retracción del flexómetro funcione correctamente.
- Técnica de Medición:
- Asegurarse de que la cinta esté recta y tensa durante la medición. Evitar dobleces o curvas que puedan afectar la precisión.
- Colocar el gancho o uña del extremo de la cinta en el punto de inicio de la medición, asegurándose de que esté bien apoyado y no se desplace.
- Extender la cinta hasta el punto final de la medición, manteniendo la tensión y la alineación.
- Leer la medida en la graduación de la cinta, justo en el punto donde coincide con el borde del objeto o la marca de referencia.
- Si es necesario, utilizar un lápiz o marcador para marcar el punto de medición.
- Realizar varias mediciones para verificar la consistencia y reducir el error aleatorio.
- Precauciones:
- Evitar medir en condiciones de viento fuerte, ya que la cinta puede moverse y afectar la precisión.
- Evitar medir sobre superficies calientes, ya que la cinta puede dilatarse y afectar la precisión.
- Tener cuidado al medir cerca de bordes afilados o puntiagudos, ya que la cinta puede dañarse.
- No dejar caer el flexómetro ni golpearlo, ya que esto puede afectar su precisión.
- Retraer la cinta del flexómetro lentamente para evitar que se enrede o se dañe.
- Mantenimiento:
- Limpiar la cinta después de cada uso, eliminando el polvo, la suciedad y la humedad.
- Lubricar el mecanismo de retracción del flexómetro periódicamente.
- Guardar el flexómetro o cinta métrica en un lugar seco y protegido del polvo y la humedad.
Aunque el uso de flexómetros y cintas métricas es relativamente sencillo, es importante que los trabajadores reciban capacitación sobre las técnicas correctas de medición y las precauciones que deben tomar para obtener mediciones precisas y evitar errores.
Uso de Calibradores (Vernier, Pie de Rey): Medición Precisa de Dimensiones Pequeñas
Los calibradores, también conocidos como pie de rey o vernier, son instrumentos de medición de alta precisión que se utilizan para medir dimensiones pequeñas, como diámetros interiores y exteriores, profundidades y espesores de objetos. Los calibradores son herramientas esenciales en el montaje de estructuras metálicas para verificar las dimensiones de pernos, tuercas, agujeros, ranuras y otros elementos de precisión.
Existen diferentes tipos de calibradores:
- Calibrador Vernier: Es el calibrador más común. Consiste en una regla fija con una escala principal y una corredera móvil con una escala vernier (nonio) que permite leer fracciones de la unidad de medida principal. Los calibradores vernier pueden ser analógicos (con escalas graduadas) o digitales (con pantalla digital).
- Calibrador con Reloj Comparador: En lugar de una escala vernier, tiene un reloj comparador que muestra la medida en una aguja.
- Calibrador de Profundidad: Se utiliza para medir la profundidad de agujeros, ranuras y rebajes.
- Calibrador de Altura: Se utiliza para medir la altura de objetos o para trazar líneas de referencia.
Para utilizar un calibrador vernier correctamente, se deben seguir los siguientes pasos:
- Limpieza: Limpiar las superficies de medición del calibrador y del objeto a medir.
- Cero: Verificar que el calibrador esté en cero cuando las mordazas estén cerradas. Si no es así, ajustarlo.
- Posicionamiento: Colocar el objeto a medir entre las mordazas del calibrador, asegurándose de que esté bien apoyado y alineado.
- Ajuste: Cerrar las mordazas del calibrador suavemente sobre el objeto, sin apretar demasiado.
- Bloqueo: Bloquear el tornillo de fijación de la corredera para evitar que se mueva durante la lectura.
- Lectura:
- Escala Principal: Leer el valor en la escala principal, justo antes del cero de la escala vernier.
- Escala Vernier: Buscar la línea de la escala vernier que coincida exactamente con una línea de la escala principal. El valor de esta línea en la escala vernier se suma al valor de la escala principal.
- Calibradores Digitales: Simplemente leer el valor que se muestra en la pantalla digital.
- Repetición: Repetir la medición varias veces para verificar la consistencia y reducir el error aleatorio.
Algunas precauciones y recomendaciones para el uso de calibradores son:
- Utilizar el calibrador adecuado para el tipo de medición y el tamaño del objeto.
- No forzar el calibrador ni utilizarlo para fines para los que no fue diseñado.
- Evitar golpear o dejar caer el calibrador, ya que esto puede afectar su precisión.
- Proteger el calibrador del polvo, la humedad y las temperaturas extremas.
- Guardar el calibrador en su estuche cuando no se esté utilizando.
- Calibrar el calibrador periódicamente.
La apreciación de un calibrador, es la mínima medida que puede ofrecer.
Es fundamental que los trabajadores que utilizan calibradores reciban capacitación específica sobre su uso correcto, la lectura de las escalas, la interpretación de los resultados y las precauciones que deben tomar para obtener mediciones precisas y confiables.
Tolerancias Dimensionales: Límites Aceptables de Variación
En el montaje de estructuras metálicas, como en cualquier proceso de fabricación y construcción, es imposible obtener dimensiones perfectas. Siempre habrá una cierta variación entre la dimensión nominal (la dimensión especificada en el plano o diseño) y la dimensión real (la dimensión obtenida después de la fabricación o el montaje). Las tolerancias dimensionales definen los límites aceptables de esta variación.
Una tolerancia dimensional es la variación permitida en una dimensión específica. Se expresa como una desviación máxima y mínima con respecto a la dimensión nominal. Por ejemplo, una dimensión de 100 mm con una tolerancia de ±0.5 mm significa que la dimensión real puede estar entre 99.5 mm y 100.5 mm.
Las tolerancias dimensionales son importantes por varias razones:
- Funcionalidad: Aseguran que las piezas encajen y funcionen correctamente. Por ejemplo, si un perno es demasiado grande o demasiado pequeño para un agujero, no podrá ensamblarse correctamente.
- Intercambiabilidad: Permiten que las piezas fabricadas en diferentes lugares o por diferentes proveedores sean intercambiables.
- Calidad: Controlan la calidad de la fabricación y el montaje, asegurando que las piezas cumplan con los requisitos especificados.
- Costo: Las tolerancias más estrictas (más pequeñas) generalmente implican costos de fabricación más altos, ya que requieren mayor precisión en los procesos y en los instrumentos de medición. Por lo tanto, es importante establecer tolerancias que sean lo suficientemente estrictas para asegurar la funcionalidad y la calidad, pero no más estrictas de lo necesario.
Las tolerancias dimensionales se especifican en los planos y en las especificaciones técnicas del proyecto. Existen diferentes formas de expresar las tolerancias, como:
- Tolerancia Bilateral: La desviación se expresa como un valor positivo y negativo con respecto a la dimensión nominal (p. ej., 100 ± 0.5 mm).
- Tolerancia Unilateral: La desviación se expresa en una sola dirección (p. ej., 100 +0.5 / -0 mm, o 100 +0 / -0.5 mm).
- Tolerancia Geométrica: Especifica la variación permitida en la forma, la orientación o la posición de un elemento geométrico (p. ej., rectitud, planitud, perpendicularidad, paralelismo, concentricidad).
- Ajustes y Tolerancias: En el caso de piezas que deben encajar entre sí (p. ej., un perno y un agujero), se utilizan sistemas de ajustes y tolerancias que definen las tolerancias tanto del eje (perno) como del agujero.
Es fundamental que los trabajadores que realizan el montaje de estructuras metálicas comprendan el concepto de tolerancias dimensionales, sepan interpretar las tolerancias especificadas en los planos y utilicen los instrumentos de medición adecuados para verificar que las dimensiones reales de las piezas estén dentro de los límites de tolerancia.
Existen normas, como por ejemplo la ISO 2768, que habla de tolerancias generales.
Errores Comunes en la Medición: Identificación y Prevención
Incluso con los instrumentos de medición adecuados y la capacitación correcta, es posible cometer errores en la medición. Los errores pueden ser causados por diversos factores, como:
- Errores Sistemáticos: Son errores que se repiten de forma consistente en la misma dirección y magnitud. Pueden ser causados por:
- Instrumento mal calibrado.
- Defectos en el instrumento.
- Uso de un instrumento inadecuado para la tarea.
- Factores ambientales (p. ej., temperatura, humedad).
- Errores Aleatorios: Son errores que varían de forma impredecible en magnitud y dirección. Pueden ser causados por:
- Limitaciones en la precisión del instrumento.
- Variaciones en las condiciones de medición.
- Errores de lectura o interpretación del operador.
- Errores de Paralaje: Son errores que se producen cuando el observador no mira perpendicularmente a la escala del instrumento, lo que provoca una lectura incorrecta.
- Errores de Aplicación de Fuerza: Son errores que se producen cuando se aplica demasiada o muy poca fuerza al utilizar un instrumento de medición (p. ej., apretar demasiado un calibrador).
- Errores de Posicionamiento: Son errores que se producen cuando el instrumento de medición no se coloca correctamente en relación con el objeto a medir.
- Errores de Interpretación: Son errores que se producen cuando el operador no interpreta correctamente la lectura del instrumento o las especificaciones técnicas.
- Errores de Cálculo: Son errores que se producen al realizar cálculos con los valores medidos.
- Errores de Transcripción: Son errores que se producen al copiar o registrar los valores medidos.
Para prevenir y minimizar los errores en la medición, se deben seguir las siguientes recomendaciones:
- Utilizar el instrumento de medición adecuado para la tarea y para el nivel de precisión requerido.
- Verificar que el instrumento esté calibrado y en buen estado.
- Limpiar las superficies de medición del instrumento y del objeto a medir.
- Seguir los procedimientos correctos para el uso de cada instrumento.
- Realizar varias mediciones de la misma magnitud y calcular el promedio.
- Evitar los errores de paralaje mirando perpendicularmente a la escala del instrumento.
- Aplicar la fuerza adecuada al utilizar el instrumento.
- Posicionar correctamente el instrumento en relación con el objeto a medir.
- Leer e interpretar correctamente las escalas y las unidades de medida.
- Realizar los cálculos con cuidado y verificar los resultados.
- Registrar las mediciones de forma clara y precisa, utilizando las unidades de medida correctas.
- Controlar los factores ambientales que puedan afectar la precisión de las mediciones (p. ej., temperatura, humedad, vibraciones).
- Recibir capacitación adecuada en el uso de instrumentos de medición y en la interpretación de resultados.
Es importante que los trabajadores sean conscientes de los posibles errores en la medición y que tomen las medidas necesarias para prevenirlos. Si se detecta un error, se debe identificar la causa y tomar medidas correctivas para evitar que se repita.
Documentación de Mediciones: Registrando la Información de Forma Clara y Precisa
La documentación de las mediciones es un aspecto fundamental de la metrología y del control de calidad en el montaje de estructuras metálicas. Registrar las mediciones de forma clara, precisa y completa permite:
- Verificar que las dimensiones y otros parámetros de los elementos estructurales cumplen con las especificaciones técnicas y las tolerancias establecidas.
- Tener un registro de las mediciones realizadas, que puede ser útil para la trazabilidad, el control de calidad, la resolución de problemas y la toma de decisiones.
- Demostrar el cumplimiento de las normas y los requisitos del proyecto.
- Facilitar la comunicación y la colaboración entre los diferentes miembros del equipo (ingenieros, supervisores, montadores, inspectores de calidad).
La documentación de las mediciones debe incluir, como mínimo, la siguiente información:
- Identificación del Proyecto: Nombre del proyecto, número de contrato, ubicación, etc.
- Identificación del Elemento Medido: Nombre o código del elemento estructural medido (p. ej., viga V-101, columna C-205, etc.).
- Fecha y Hora de la Medición: Fecha y hora en que se realizó la medición.
- Nombre del Operador: Nombre de la persona que realizó la medición.
- Instrumento de Medición Utilizado: Tipo, marca, modelo y número de serie del instrumento de medición utilizado.
- Fecha de Calibración del Instrumento: Fecha de la última calibración del instrumento de medición.
- Magnitud Medida: Descripción de la magnitud medida (p. ej., longitud, ancho, altura, diámetro, ángulo, etc.).
- Unidad de Medida: Unidad de medida utilizada (p. ej., milímetros, centímetros, metros, pulgadas, grados).
- Valor Nominal: Valor nominal de la magnitud medida, según el plano o la especificación técnica.
- Tolerancia: Tolerancia permitida para la magnitud medida.
- Valor Medido: Valor obtenido en la medición.
- Desviación: Diferencia entre el valor medido y el valor nominal.
- Conformidad: Indicar si la medición cumple o no con la tolerancia establecida (p. ej., "Conforme" o "No Conforme").
- Observaciones: Cualquier observación relevante sobre la medición (p. ej., condiciones ambientales, dificultades encontradas, etc.).
- Firma del Operador: Firma de la persona que realizó la medición.
- Firma del Supervisor (si aplica): Firma del supervisor que revisó y aprobó la medición.
Las mediciones se pueden registrar en diferentes formatos, como:
- Formatos de Inspección: Formularios preimpresos o electrónicos diseñados específicamente para registrar las mediciones de un determinado tipo de elemento o tarea.
- Hojas de Cálculo: Tablas en programas como Excel, donde se pueden registrar y analizar los datos de medición.
- Software de Gestión de Calidad: Programas informáticos especializados en la gestión de la calidad, que permiten registrar, analizar y generar informes sobre las mediciones.
- Libretas de Campo: Cuadernos donde los operadores pueden registrar las mediciones de forma manual.
Es importante que la documentación de las mediciones sea clara, legible, completa y precisa. Se deben utilizar formatos estandarizados y se debe capacitar a los trabajadores en su correcto uso. La documentación de las mediciones debe ser archivada y conservada durante el tiempo que establezca la normatividad o los requisitos del proyecto.
Mantenimiento de Instrumentos de Medición: Cuidando las Herramientas de la Precisión
Los instrumentos de medición son herramientas delicadas y costosas que requieren un cuidado y mantenimiento adecuados para garantizar su precisión, prolongar su vida útil y evitar errores en las mediciones. El mantenimiento de los instrumentos de medición debe ser una parte integral del programa de control de calidad en el montaje de estructuras metálicas.
El mantenimiento de los instrumentos de medición incluye las siguientes actividades:
- Limpieza:
- Limpiar los instrumentos de medición después de cada uso, eliminando el polvo, la suciedad, la grasa y los residuos de material.
- Utilizar un paño suave y seco, o un paño ligeramente humedecido con un producto de limpieza adecuado para el tipo de instrumento.
- No utilizar disolventes fuertes ni productos abrasivos que puedan dañar el instrumento.
- Secar completamente el instrumento después de limpiarlo.
- Almacenamiento:
- Guardar los instrumentos de medición en un lugar limpio, seco, seguro y protegido del polvo, la humedad, los golpes, las vibraciones y las temperaturas extremas.
- Utilizar estuches, cajas o armarios especiales para guardar los instrumentos.
- No almacenar los instrumentos de medición junto con herramientas u objetos que puedan dañarlos.
- Guardar los instrumentos de medición en una posición estable para evitar que se caigan o se golpeen.
- Manipulación:
- Manipular los instrumentos de medición con cuidado, evitando golpes, caídas y vibraciones.
- No forzar los instrumentos ni utilizarlos para fines para los que no fueron diseñados.
- Utilizar guantes limpios al manipular instrumentos de alta precisión para evitar la transferencia de grasa o suciedad de las manos.
- Verificación Periódica:
- Verificar periódicamente el estado y la precisión de los instrumentos de medición, utilizando patrones de referencia o comparándolos con otros instrumentos calibrados.
- Si se detecta algún daño, defecto o desviación en la precisión, el instrumento debe ser retirado de servicio y enviado a reparación o calibración.
- Lubricación (si aplica):
- Algunos instrumentos de medición, como los calibradores o los micrómetros, requieren lubricación periódica de sus partes móviles.
- Utilizar el lubricante recomendado por el fabricante y seguir las instrucciones de lubricación.
- Calibración:
- Calibrar los instrumentos de medición periódicamente, según lo establecido en el plan de calibración de la empresa o las recomendaciones del fabricante.
- La calibración debe ser realizada por personal capacitado y utilizando patrones de referencia trazables a patrones nacionales o internacionales.
- Reparación:
- Si un instrumento de medición se daña o se desajusta, debe ser reparado por personal calificado.
- No intentar reparar un instrumento de medición si no se tiene la capacitación y las herramientas adecuadas.
- Registro:
- Llevar un registro del mantenimiento de cada instrumento de medición, incluyendo la fecha de limpieza, lubricación, verificación, calibración y reparación.
- Este registro puede ser útil para la trazabilidad, el control de calidad y la planificación del mantenimiento.
Es importante que los trabajadores que utilizan instrumentos de medición reciban capacitación sobre su correcto cuidado y mantenimiento. La empresa debe proporcionar los recursos necesarios (productos de limpieza, lubricantes, estuches, etc.) para el mantenimiento de los instrumentos y debe establecer procedimientos claros para su cuidado y conservación.
Tabla de Instrumentos de Medición Comunes en el Montaje de Estructuras Metálicas
Instrumento | Uso Principal | Tipos | Precauciones |
---|---|---|---|
Flexómetro (cinta métrica retráctil) | Medir longitudes, anchos, alturas. | De acero, de fibra de vidrio. |
|
Cinta métrica | Medir longitudes. | De acero, de fibra de vidrio. |
|
Nivel de burbuja | Verificar la horizontalidad o verticalidad de una superficie. | De burbuja simple, de doble burbuja, láser. |
|
Calibrador (Vernier, Pie de Rey) | Medir dimensiones pequeñas (diámetros, profundidades, espesores). | Analógico (con escala vernier), digital, con reloj comparador. |
|
Teodolito | Medir ángulos horizontales y verticales. | Óptico, electrónico. |
|
Estación Total | Medir ángulos, distancias y coordenadas. | Convencional, robótica. |
|
Plomada | Verificar la verticalidad de un elemento. | De punta, esférica. |
|
Tabla de Errores Comunes en la Medición y su Prevención
Error | Causa | Prevención |
---|---|---|
Error de paralaje | No mirar perpendicularmente a la escala del instrumento. | Alinear el ojo con la marca de la escala y el punto de medición. |
Error por temperatura | Dilatación o contracción del instrumento o del objeto medido debido a cambios de temperatura. | Realizar las mediciones a una temperatura ambiente estable y conocida. Utilizar instrumentos con compensación de temperatura. |
Error por fuerza excesiva | Aplicar demasiada fuerza al utilizar el instrumento (p. ej., apretar demasiado un calibrador). | Utilizar la fuerza adecuada para cada instrumento. No forzar el instrumento. |
Error de cero | El instrumento no marca cero cuando debería. | Verificar y ajustar el cero del instrumento antes de cada uso. |
Error de lectura | Lectura incorrecta de la escala. |
|
Tabla de Unidades de Medida Comunes en el Montaje de Estructuras Metálicas
Magnitud | Unidad (Sistema Internacional - SI) | Símbolo | Otras Unidades Comunes |
---|---|---|---|
Longitud | Metro | m | Milímetro (mm), centímetro (cm), pulgada (in), pie (ft). |
Ángulo | Radián | rad | Grado sexagesimal (°), minuto ('), segundo ("). |
Masa | Kilogramo | kg | Tonelada (t), libra (lb). |
Fuerza | Newton | N | Kilopondio (kp), libra fuerza (lbf). |
Presión | Pascal | Pa | Bar, kilogramo por centímetro cuadrado (kg/cm²), libra por pulgada cuadrada (psi). |
Tabla de Tolerancias Dimensionales (Ejemplo)
Dimensión Nominal (mm) | Tolerancia (mm) | Dimensión Máxima (mm) | Dimensión Mínima (mm) | Tipo de Tolerancia |
---|---|---|---|---|
100 | ± 0.5 | 100.5 | 99.5 | Bilateral |
50 | +0.2 / -0 | 50.2 | 50.0 | Unilateral |
25 | +0 / -0.1 | 25.0 | 24.9 | Unilateral |
Nota: Estos son solo ejemplos. Las tolerancias dimensionales reales deben ser especificadas en los planos y en las especificaciones técnicas del proyecto.
Importancia de la Metrología en la Norma Sismo Resistente Colombiana (NSR-10)
La Norma Sismo Resistente Colombiana (NSR-10) establece los requisitos mínimos para el diseño y construcción de edificaciones en Colombia, con el objetivo de proteger la vida y el patrimonio de las personas en caso de un sismo. La NSR-10 incluye requisitos específicos para el diseño y construcción de estructuras metálicas, y la metrología juega un papel fundamental en el cumplimiento de estos requisitos.
Algunos aspectos de la NSR-10 donde la metrología es crucial son:
- Dimensiones de los Elementos Estructurales: La NSR-10 establece requisitos para las dimensiones mínimas de los elementos estructurales (vigas, columnas, placas, etc.) y para las tolerancias dimensionales permitidas. La metrología se utiliza para verificar que las dimensiones reales de los elementos cumplan con estos requisitos.
- Conexiones: La NSR-10 establece requisitos para el diseño y la ejecución de las conexiones entre los elementos estructurales (soldaduras, pernos, remaches). La metrología se utiliza para verificar que las dimensiones de las conexiones, la longitud y calidad de las soldaduras, el apriete de los pernos, etc., cumplan con los requisitos especificados.
- Alineación y Plomada: La NSR-10 establece requisitos para la alineación y la plomada de los elementos estructurales. La metrología se utiliza para verificar que los elementos estén correctamente alineados y aplomados, dentro de las tolerancias permitidas.
- Control de Calidad: La NSR-10 exige la implementación de un programa de control de calidad que incluya la inspección y el ensayo de los materiales y los procesos de construcción. La metrología es una herramienta fundamental para el control de calidad, ya que permite verificar que los materiales y los procesos cumplan con los requisitos establecidos.
El incumplimiento de los requisitos de la NSR-10, incluyendo los relacionados con la metrología, puede tener consecuencias graves, como la reducción de la resistencia y la estabilidad de la estructura, el aumento del riesgo de colapso en caso de un sismo y la imposición de sanciones legales a los responsables del proyecto.
La NSR-10, en su Título F, establece los parámetros para las estructuras metálicas.
Formato de Registro de Mediciones (Ejemplo)
REGISTRO DE MEDICIONES | |||
---|---|---|---|
Proyecto: [Nombre del Proyecto] Ubicación: [Ubicación del Proyecto] | |||
Elemento Medido: [Nombre o código del elemento] | Fecha: [Fecha de la medición] | Hora: [Hora de la medición] | Operador: [Nombre del operador] |
Instrumento: [Tipo, marca y modelo del instrumento] | No. Serie: [Número de serie del instrumento] | Última Calibración: [Fecha de la última calibración] | |
Magnitud Medida | Unidad | Valor Nominal | Tolerancia |
[Descripción de la magnitud] | [Unidad de medida] | [Valor nominal] | [Tolerancia] |
Mediciones | |||
Medición 1 | Medición 2 | Medición 3 | Promedio |
[Valor de la medición 1] | [Valor de la medición 2] | [Valor de la medición 3] | [Promedio de las mediciones] |
Desviación: [Desviación del promedio con respecto al valor nominal] | Conformidad: [Indicar si la medición cumple o no con la tolerancia] | ||
Observaciones: [Cualquier observación relevante sobre la medición] | |||
Firma del Operador: | Firma del Supervisor: |
Construcción de Pérgolas Metálicas Industriales
Diseño y Montaje
de Estructuras
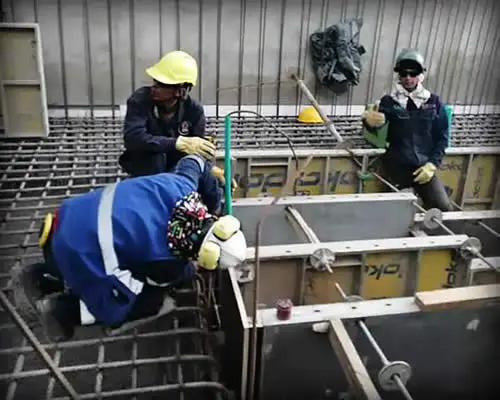
MIC SAS. fábrica e instala una variedad de pérgolas metálicas industriales de acero a la medida de cada cliente. Todas nuestras pérgolas de metal son de ingeniería y resistencia industrial y están hechas para perdurar en el tiempo. Cada de una de nuestras entregas son totalmente personalizables. Consulte nuestras imágenes de ejemplo y póngase en contacto con nosotros para discutir sus requisitos.
VER MÁS INFORMACIÓNEstructuras Industriales para Puentes
Construcción en
Acero Estructural
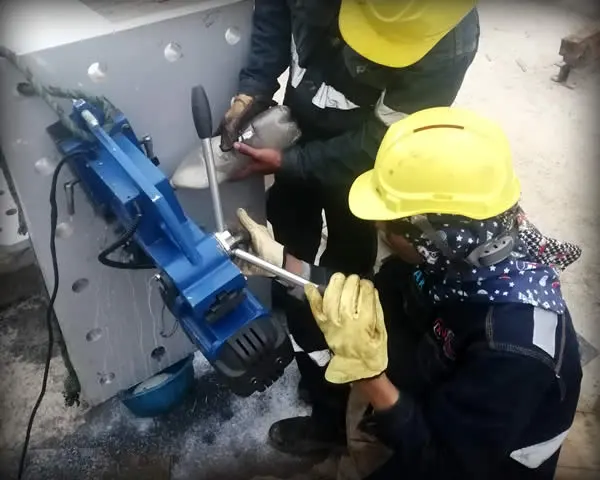
Los puentes de acero se utilizan ampliamente en todo el mundo en diferentes formas estructurales con diferente longitud de tramo, como puentes de carreteras, puentes ferroviarios y pasarelas. Entre los materiales para puentes vehiculares y peatonales, el acero tiene las cualidades de resistencia más altas, adecuadas y favorables. Los puentes de acero duran más que otros tipos de construcción de puentes.
VER MÁS INFORMACIÓNTechos y Cubiertas con Estructura Metálica
Diseño, Fabricación
y Montaje
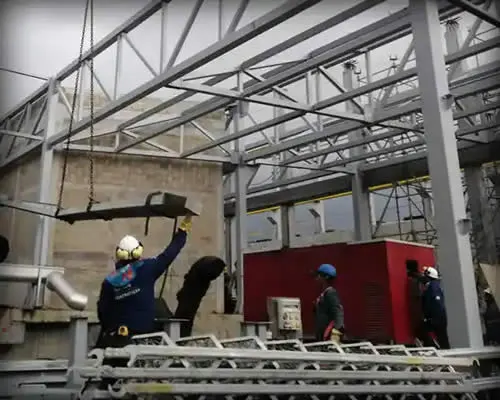
Nuestra vocación por la satisfacción total de cada cliente nos lleva a abordar cada proyecto con dedicación, buscando la “precisión milimétrica” en cada detalle, ofreciendo servicios personalizados y optimizando nuestras soluciones de ingeniería para lograr la máxima calidad en todos nuestros techos y cubiertas metálicas con estructura en acero. Implantamos herramientas de software avanzadas integradas a cada diseño.
VER MÁS INFORMACIÓNCanopys, Plataformas y Escaleras Metálicas
Ingeniería y Cálculo
Estructural
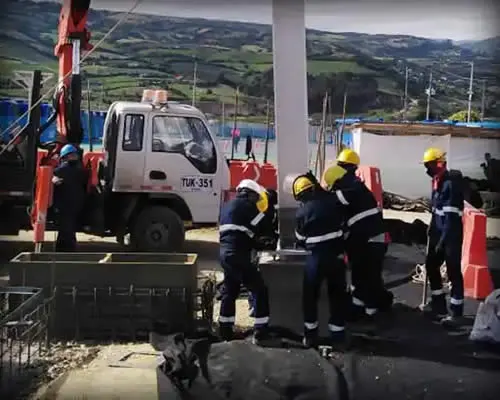
La calidad de MIC SAS. se refleja en la gran diversidad de obras y proyectos que producimos. Realizamos el diseño y construcción de todo tipo de estructuras para Canopys, Plataformas y Escaleras industriales en toda Colombia. Para repasar nuestra versatilidad, siempre damos conocer a cada cliente, ejemplos y casos de exito de nuestras construcciones más recientes.
VER MÁS INFORMACIÓNInformación
-
- Bogotá, Colombia
- Fijo: (57) 60-1 9401441
- Celular: (57) 311 5313815
- Horario de Atención: Lunes a Viernes de 7:00 am - 6:00pm
Sábado de 7:00 am - 1:00pm - Click acá para enviarnos tus mensajes a:
- (57) 311 5313815
Nuestros Servicios
Nuestra Empresa
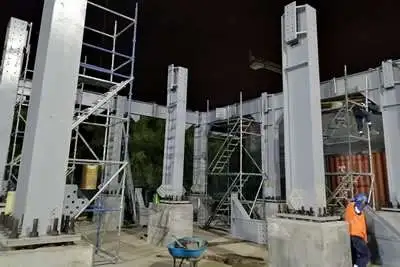
Resulta muy grato para nuestra empresa Montajes Ingeniería y Construcción SAS, trabajar en proyectos civiles construidos en acero, trabajando muy a gusto con diferentes metales de excelente calidad en Bogotá, Colombia. Nos esmeramos y estamos comprometidos con la limpieza, salud y seguridad en el sitio de levantamiento de toda edificación y gestionamos a todas luces de forma explícita, estudios y cálculos estructurales en cada proyecto. Pasamos por estructuras verdaderamente elementales a esqueletos y armazones metálicos industriales realmente complejos, apasionados por el gusto y el diseño de elementos y componentes arquitectónicos vanguardistas.
Leer más
Nuestra Ventaja
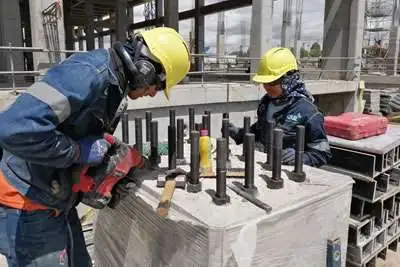
DEFINIMOS TÉRMINOS IMPORTANTES QUE SE EMPLEAN EN EL MUNDO DE LAS ESTRUCTURAS METÁLICAS:
Mostramos las características inmejorables del metal como material de construcción y de los diversos tipos de acero que se trabajan en Colombia. Todos los perfiles, columnas, vigas, cerchas, techos y demás componentes estructurales que fabricamos, cumplen rigurosamente con todas las regulaciones y parámetros de diseño colombianos e internacionales. Los componentes que conforman nuestras estructuras metálicas, soportan correctamente y con insuperable perfección, todas las cargas y fuerzas ejercidas sobre la edificación.
Leer más