Sistemas de Protección Anticorrosiva Aplicados Rigurosamente en Taller para Vigas Prefabricadas de Acero: Garantía de Calidad, Durabilidad y Eficiencia Superior en Proyectos de Construcción Metálica en Bogotá y Toda Colombia.
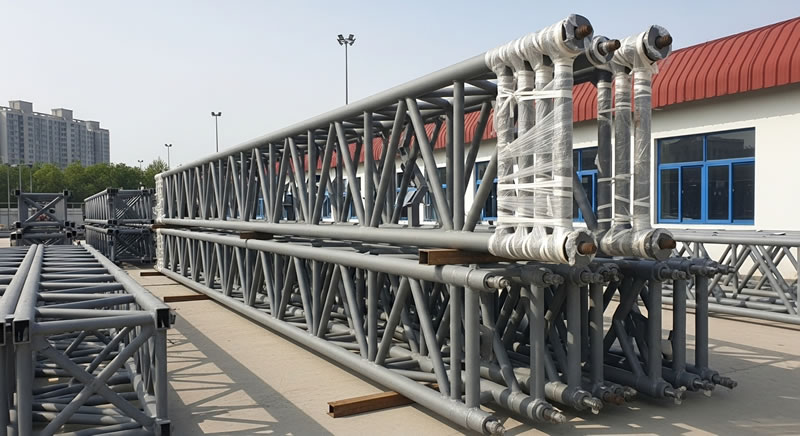
La protección contra la corrosión de las vigas metálicas prefabricadas, un componente esencial dentro de la categoría más amplia de vigas de acero armadas o fabricadas, representa una fase crítica en el ciclo de vida de cualquier estructura metálica. La aplicación de estos sistemas de protección en un entorno controlado de taller, antes de que las vigas sean transportadas al sitio de construcción, ofrece ventajas significativas en términos de calidad, uniformidad, durabilidad y eficiencia del proyecto. Este enfoque meticuloso asegura que cada viga prefabricada reciba un tratamiento óptimo, preparado para resistir las condiciones ambientales específicas a las que estará expuesta, ya sea en el clima variable de Bogotá o en otras regiones de Colombia con diferentes grados de agresividad atmosférica.
La implementación de sistemas anticorrosivos en taller es un proceso multifacético que involucra una secuencia de operaciones cuidadosamente planificadas y ejecutadas, desde la preparación inicial de la superficie hasta la aplicación final del recubrimiento y los controles de calidad subsecuentes. Cada paso es fundamental para lograr un desempeño a largo plazo y evitar fallos prematuros que podrían comprometer la integridad estructural y la seguridad de la edificación.
Preparación Meticulosa de la Superficie: La Base Esencial para una Protección Duradera
El éxito de cualquier sistema de protección anticorrosiva depende intrínsecamente de la calidad de la preparación de la superficie del acero. La eliminación completa de contaminantes como óxido, calamina (escama de laminación), aceite, grasa, polvo y sales solubles es indispensable para asegurar una adherencia óptima del recubrimiento y prevenir la corrosión subyacente. En el entorno controlado del taller, se emplean diversos métodos de preparación de superficie, siendo el chorreado abrasivo el más común y efectivo para vigas prefabricadas de acero.
Chorreado Abrasivo: Limpieza y Perfil de Anclaje Óptimos
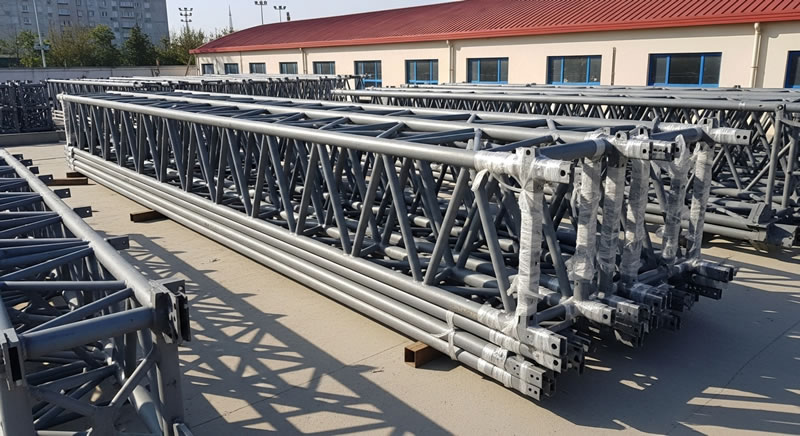
El chorreado abrasivo, también conocido como limpieza con chorro de abrasivo o "sandblasting" (aunque la arena de sílice está restringida en muchos lugares por razones de salud), utiliza partículas abrasivas impulsadas a alta velocidad contra la superficie de acero. Este proceso no solo limpia la superficie hasta el grado especificado, sino que también crea un perfil de rugosidad o "perfil de anclaje". Este perfil microscópico es vital porque aumenta el área superficial y proporciona un anclaje mecánico para la primera capa de recubrimiento (imprimación), mejorando significativamente la adherencia.
Los grados de limpieza por chorreado abrasivo se definen comúnmente según estándares internacionales como los de la Sociedad de Recubrimientos Protectores (SSPC) y la Organización Internacional de Normalización (ISO 8501-1). La selección del grado adecuado depende de las especificaciones del proyecto, el tipo de recubrimiento a aplicar y las condiciones de servicio esperadas. Algunos de los grados más utilizados en taller para vigas prefabricadas son:
- SSPC-SP 5 / NACE N°1 / Sa 3 (Limpieza con Chorro Abrasivo hasta Metal Blanco): El grado más alto de limpieza. Elimina toda la calamina, óxido, pintura y materia extraña visible. La superficie debe tener una apariencia metálica blanca uniforme. Se especifica para condiciones de servicio severas o cuando se requiere el máximo rendimiento del recubimiento, como en ambientes C4 o C5.
- SSPC-SP 10 / NACE N°2 / Sa 2½ (Limpieza con Chorro Abrasivo hasta Metal Casi Blanco): Elimina al menos el 95% de la calamina, óxido, pintura y materia extraña visible por cada unidad de área. Se permiten ligeras sombras, rayas o decoloraciones residuales. Es un grado muy común y proporciona una excelente base para la mayoría de los sistemas de recubrimiento de alto rendimiento. Es frecuentemente especificado para proyectos importantes en ciudades como Bogotá.
- SSPC-SP 6 / NACE N°3 / Sa 2 (Limpieza con Chorro Abrasivo Comercial): Elimina al menos dos tercios de la calamina, óxido, pintura y materia extraña visible por cada unidad de área. Se permiten manchas ligeras y sombras uniformemente distribuidas. Adecuado para ambientes de corrosividad moderada y ciertos tipos de recubrimientos.
- SSPC-SP 7 / NACE N°4 / Sa 1 (Limpieza con Chorro Abrasivo Ráfaga): Elimina óxido suelto, calamina suelta y pintura suelta. Deja óxido, calamina y pintura firmemente adheridos. Usado para limpiezas menos críticas o como preparación para repintado sobre recubrimientos existentes compatibles.
A continuación, se presenta una descripción comparativa de los grados de preparación de superficie por chorreado abrasivo más comunes según SSPC e ISO 8501-1, relevantes para las vigas prefabricadas en taller.
Estándar SSPC | Estándar ISO 8501-1 | Descripción General | Apariencia Visual | Aplicaciones Típicas para Vigas Prefabricadas |
---|---|---|---|---|
SSPC-SP 5 | Sa 3 | Limpieza hasta Metal Blanco | Superficie metálica blanca, uniforme, libre de toda contaminación visible. | Ambientes muy agresivos (C5), inmersión, recubrimientos de altas prestaciones (ej. metalización). Máxima durabilidad requerida. |
SSPC-SP 10 | Sa 2½ | Limpieza hasta Metal Casi Blanco | Eliminación del 95% de contaminantes. Se permiten ligeras sombras o rayas residuales. | Ambientes industriales y marinos (C4, C5-M), sistemas epóxicos y poliuretanos de alto rendimiento. Estándar de alta calidad común en Colombia para estructuras importantes. |
SSPC-SP 6 | Sa 2 | Limpieza Comercial | Eliminación del 67% de contaminantes. Manchas y sombras ligeras permitidas. | Ambientes de moderada agresividad (C3), imprimaciones alquídicas o epóxicas estándar. Buena relación costo-efectividad. |
SSPC-SP 7 | Sa 1 | Limpieza Ráfaga | Eliminación de contaminantes sueltos. Contaminantes firmemente adheridos permanecen. | Baja agresividad (C1, C2), preparación para repintado o recubrimientos de bajo espesor. Menos común para protección inicial de vigas nuevas. |
SSPC-SP 1 | - | Limpieza con Solvente | Eliminación de aceite, grasa, suciedad, sales solubles. No elimina óxido ni calamina. | Requisito previo a cualquier método mecánico de limpieza. Asegura la eliminación de contaminantes invisibles. |
Control Riguroso del Proceso de Preparación
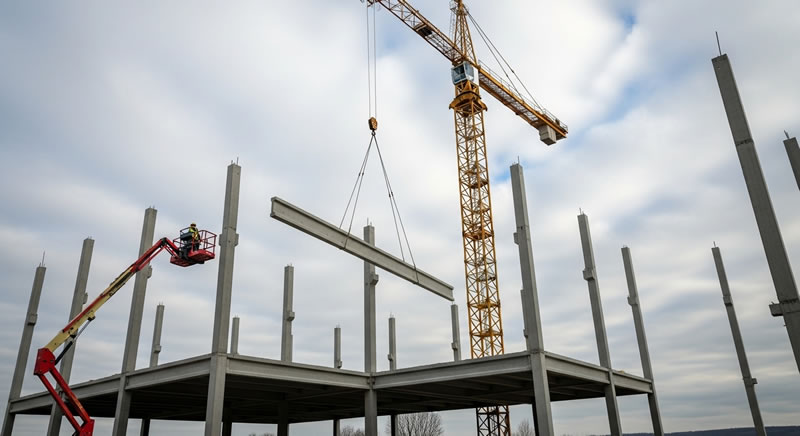
La calidad de la preparación de superficie no se logra por casualidad; requiere un control estricto durante todo el proceso en el taller. Los aspectos clave del control incluyen:
- Selección del Abrasivo: Utilizar el tipo (metálico, mineral), tamaño y forma de abrasivo adecuados para lograr el perfil de anclaje especificado sin incrustar partículas o causar daños indebidos al sustrato de acero.
- Calidad del Abrasivo: Asegurar que el abrasivo esté limpio, seco y libre de contaminantes como aceite, grasa o sales, que podrían transferirse a la superficie preparada. Se realizan pruebas periódicas de conductividad y contenido de cloruros en el abrasivo.
- Aire Comprimido: Verificar que el aire comprimido utilizado para impulsar el abrasivo esté libre de aceite y agua, utilizando filtros y secadores adecuados. La contaminación del aire puede comprometer la limpieza.
- Perfil de Anclaje: Medir y verificar regularmente la rugosidad de la superficie preparada utilizando métodos como comparadores visuales (ISO 8503-1), micrómetros de perfil (ASTM D4417 Método B) o cinta réplica (ASTM D4417 Método C). El perfil debe estar dentro del rango especificado por el fabricante del recubrimiento. Un perfil demasiado bajo reduce la adherencia, mientras que uno excesivamente alto puede dejar picos sin cubrir adecuadamente, llevando a puntos de fallo.
- Grado de Limpieza Visual: Inspeccionar visualmente la superficie inmediatamente después del chorreado, comparándola con los estándares visuales fotográficos (ISO 8501-1) o descriptivos (SSPC) correspondientes al grado especificado. La inspección debe realizarse bajo buena iluminación.
- Limpieza Final: Asegurar la eliminación de polvo y residuos de abrasivo de la superficie preparada antes de aplicar la imprimación, utilizando métodos como soplado con aire limpio y seco, aspirado o cepillado.
- Tiempo entre Preparación y Recubrimiento: Aplicar la primera capa de imprimación lo antes posible después de la preparación de la superficie, especialmente en condiciones de alta humedad como las que pueden presentarse en Bogotá o zonas costeras de Colombia. Esto evita la formación de óxido superficial instantáneo ("flash rust"), que puede comprometer la adherencia. El tiempo máximo permitido suele estar definido en las especificaciones del proyecto.
- Detección de Contaminantes No Visibles: Realizar pruebas para detectar sales solubles (cloruros, sulfatos, nitratos) en la superficie preparada, utilizando kits de prueba específicos (ej. método Bresle, ISO 8502-6 y 8502-9). Las sales higroscópicas pueden atraer humedad a través del recubrimiento y causar ampollamiento osmótico y corrosión prematura. Los límites aceptables de contaminación por sales dependen del ambiente de servicio y del sistema de recubrimiento.
Este control meticuloso en el taller asegura que la base sobre la cual se aplicará el sistema de protección anticorrosiva sea óptima, maximizando la adherencia y la vida útil del recubrimiento aplicado a las vigas prefabricadas.
Diversidad de Sistemas de Recubrimiento Aplicados en Taller
Una vez que la superficie de la viga prefabricada ha sido preparada adecuadamente, se procede a la aplicación del sistema de recubrimiento protector especificado. La elección del sistema depende de múltiples factores, incluyendo:
- El ambiente de servicio y su categoría de corrosividad (según ISO 12944).
- La vida útil esperada del sistema de protección.
- Los requerimientos estéticos (color, brillo).
- Las condiciones de aplicación y curado disponibles en el taller.
- Las especificaciones técnicas del proyecto y normativas aplicables en Colombia.
- Consideraciones de costo y ciclo de vida.
En los talleres especializados en estructuras metálicas, se dispone de la capacidad técnica y el equipamiento para aplicar una amplia gama de sistemas de recubrimiento, desde imprimaciones básicas hasta esquemas multicapa de alto rendimiento. Los tipos más comunes incluyen:
Imprimaciones Ricas en Zinc (Zinc-Rich Primers)
Estas imprimaciones contienen un alto porcentaje de polvo de zinc metálico en su formulación (típicamente >80% en película seca). Proporcionan protección catódica o galvánica al acero, similar al galvanizado, sacrificándose el zinc para proteger el sustrato de acero en caso de daño o discontinuidad en el recubrimiento. Existen dos tipos principales:
- Ricas en Zinc Inorgánico (Etil Silicato de Zinc): Ofrecen excelente resistencia a la abrasión, altas temperaturas (hasta 400°C aprox.) y solventes. Requieren un grado de limpieza muy alto (SSPC-SP 5 o SP 10) y control estricto de la humedad durante la aplicación y curado. Son una base excelente para sistemas de alto rendimiento.
- Ricas en Zinc Orgánico (Epóxicas o Poliuretanos): Son más tolerantes a grados de preparación de superficie ligeramente inferiores (SSPC-SP 6 o SP 10) y a las condiciones de aplicación. Ofrecen buena protección galvánica y son más fáciles de sobre-aplicar con capas posteriores.
Las imprimaciones ricas en zinc son frecuentemente especificadas para vigas prefabricadas destinadas a ambientes agresivos (industriales, marinos) o cuando se requiere una protección de muy larga duración.
Recubrimientos Epóxicos
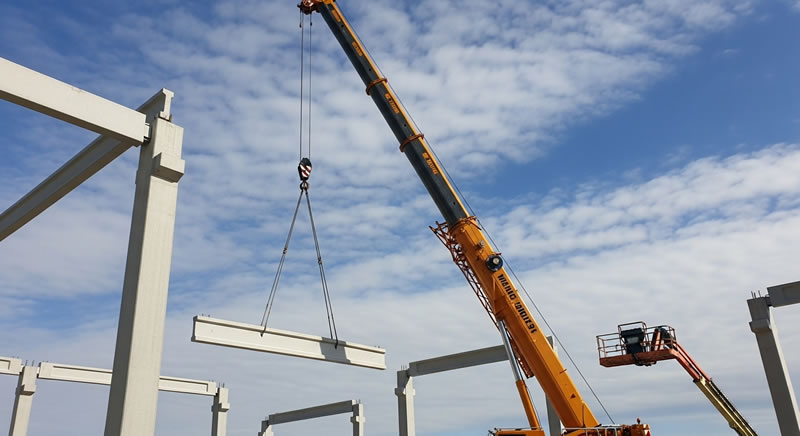
Los recubrimientos epóxicos, basados en resinas epoxi curadas con poliamidas, poliaminas o aductos, son ampliamente utilizados en la protección de estructuras de acero debido a su excelente adherencia, dureza, resistencia química y resistencia a la corrosión. Se utilizan como imprimaciones, capas intermedias y, en algunos casos, como acabado (aunque tienden a tizar con la exposición UV).
- Epoxi-Poliamida: Ofrecen buena flexibilidad, resistencia al agua y facilidad de aplicación. Son comunes como imprimaciones y capas intermedias.
- Epoxi-Poliamina: Proporcionan mayor resistencia química y curado más rápido, pero pueden ser más quebradizos.
- Epoxi Fenólico: Diseñados para una resistencia química superior, especialmente a solventes y ácidos, y para servicio a temperaturas elevadas o en inmersión.
- Epoxi Mastic: Formulaciones de altos sólidos, tolerantes a la preparación de superficie (pueden aplicarse sobre SSPC-SP 2 o SP 3 en mantenimiento, aunque para vigas nuevas se prefiere SSPC-SP 6 o SP 10). Penetran bien en superficies con óxido residual firmemente adherido y proporcionan una barrera de alto espesor.
- Epoxi Rico en Zinc: Como se mencionó anteriormente, combinan la protección de barrera epóxica con la protección galvánica del zinc.
Los sistemas multicapa basados en epóxicos son una solución robusta y versátil para una amplia gama de aplicaciones de vigas prefabricadas en Colombia.
Recubrimientos de Poliuretano
Los poliuretanos se utilizan principalmente como capas de acabado sobre imprimaciones y capas intermedias epóxicas. Su principal ventaja es su excelente resistencia a la intemperie, especialmente a la radiación ultravioleta (UV), lo que les permite retener el color y el brillo durante mucho tiempo, incluso en exteriores. También ofrecen buena resistencia química, a la abrasión y flexibilidad.
- Poliuretanos Alifáticos: Son los más utilizados como acabado exterior debido a su superior resistencia UV y retención de color/brillo.
- Poliuretanos Aromáticos: Son más económicos pero tienden a amarillear y perder brillo con la exposición UV. Se usan a veces como capas intermedias resistentes o en áreas no expuestas a la luz solar directa.
La combinación de un sistema epóxico (imprimación e intermedio) con un acabado de poliuretano alifático es un estándar de la industria para la protección duradera y estética de estructuras metálicas expuestas, incluyendo vigas prefabricadas.
Otros Tipos de Recubrimientos
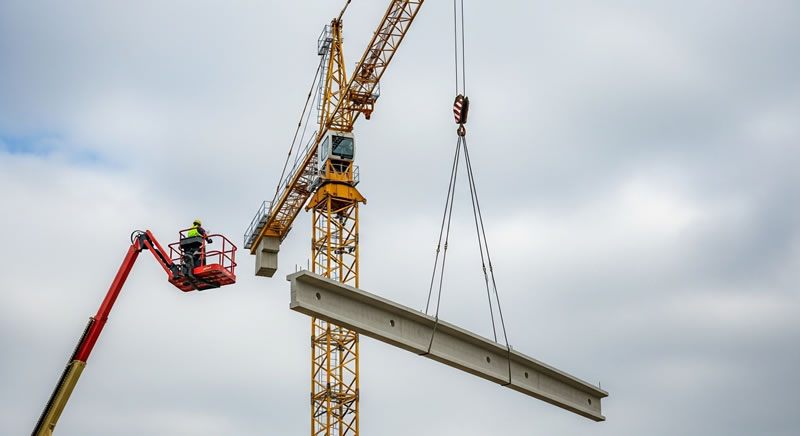
Además de los sistemas ricos en zinc, epóxicos y poliuretanos, en taller se pueden aplicar otros tipos de recubrimientos según las necesidades específicas:
- Alquídicos: Recubrimientos tradicionales a base de resinas alquídicas modificadas. Son económicos y fáciles de aplicar, pero ofrecen una protección limitada en ambientes agresivos y tienen menor durabilidad que los sistemas epóxicos/poliuretanos. Adecuados para ambientes C1 o C2.
- Polisiloxanos: Tecnología más reciente que combina la resistencia a la corrosión de los epóxicos con la resistencia a la intemperie de los poliuretanos en una sola capa (o como acabado). Ofrecen excelente retención de color y brillo, bajos VOC y larga durabilidad, aunque suelen tener un costo inicial más alto.
- Recubrimientos Intumescentes: Diseñados para la protección pasiva contra el fuego. Bajo la acción del calor, se expanden formando una capa carbonizada aislante que protege el acero del aumento rápido de temperatura durante un incendio, manteniendo la capacidad portante de la viga por un tiempo determinado. Su aplicación requiere técnicas y controles específicos.
La siguiente tabla compara algunas características clave de los tipos de recubrimientos comúnmente aplicados en taller a vigas prefabricadas.
Tipo de Recubrimiento | Función Principal | Ventajas Principales | Limitaciones Principales | Uso Típico en Vigas Prefabricadas |
---|---|---|---|---|
Rico en Zinc Inorgánico (Etil Silicato) | Imprimación (Protección Galvánica) | Excelente protección catódica, resistencia a alta T°, abrasión. Larga duración. | Requiere SSPC-SP 5/10, sensible a humedad en aplicación/curado. No flexible. | Ambientes agresivos (C4, C5), costeros, industriales. Base para sistemas de alto rendimiento. |
Rico en Zinc Orgánico (Epoxi) | Imprimación (Protección Galvánica) | Buena protección catódica, más tolerante a superficie y aplicación, fácil de sobreaplicar. | Menor resistencia a T° y abrasión que el inorgánico. | Ambientes C3-C5. Alternativa versátil al zinc inorgánico. |
Epóxico (Poliamida/Poliamina) | Imprimación / Intermedio (Barrera) | Excelente adherencia, dureza, resistencia química y al agua. Versátil. | Tiza con exposición UV (si se usa como acabado). Requiere preparación SP 6/10. | Sistemas multicapa para ambientes C2-C5. Protección robusta estándar. |
Epóxico Mastic | Imprimación / Intermedio (Barrera) | Altos sólidos, alto espesor, tolerante a superficie (en mantenimiento), buena protección de bordes. | Puede tener menor resistencia química que epóxicos estándar. Tiza con UV. | Repintado, superficies difíciles, búsqueda de alto espesor en menos capas. |
Poliuretano Alifático | Acabado (Estético y Protector) | Excelente resistencia UV, retención de color y brillo, buena resistencia química y a abrasión. | Requiere imprimación/intermedio adecuado. Costo mayor que alquídicos. | Capa final sobre sistemas epóxicos para exposición exterior en ambientes C2-C5. Acabado duradero y estético. |
Alquídico | Imprimación / Acabado (Barrera) | Bajo costo, fácil aplicación, buena humectación. | Baja resistencia química y a la humedad, menor durabilidad en exteriores, saponifica sobre zinc. | Ambientes de baja agresividad (C1, C2). Proyectos con presupuesto limitado. Interiores. |
Polisiloxano | Intermedio / Acabado (Barrera y Estético) | Combina protección epóxica y resistencia UV de poliuretano, excelente retención color/brillo, bajos VOC. | Costo inicial más alto. Puede requerir técnicas de aplicación específicas. | Sistemas de alto rendimiento y larga duración (C4, C5), reducción de capas. Proyectos sostenibles. |
Intumescente | Protección Pasiva Contra Fuego | Proporciona resistencia al fuego certificada, acabado estético posible. | Requiere aplicación especializada, control de espesores crítico, protección adicional contra humedad/ambiente. | Vigas que requieren cumplir normativas de seguridad contra incendios (ej. NSR-10 en Colombia). |
La selección y aplicación correcta de estos sistemas en el ambiente controlado del taller asegura que las vigas prefabricadas lleguen a obra con una protección anticorrosiva de alta calidad, listas para su montaje.
Galvanizado en Caliente: Protección Robusta por Inmersión
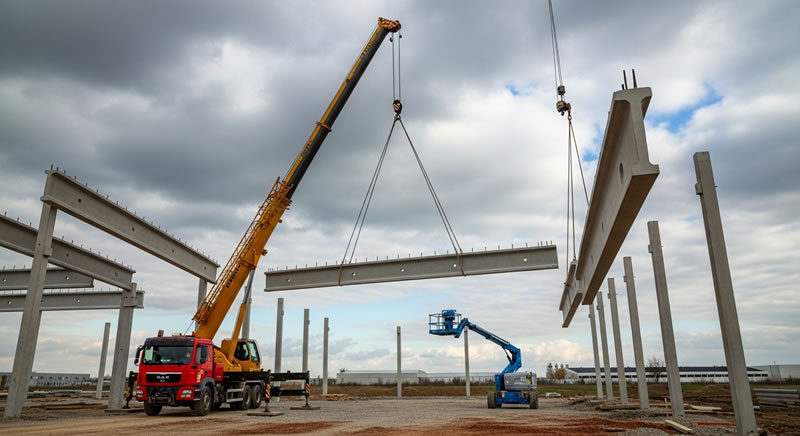
Además de los sistemas de recubrimiento líquido (pinturas), el galvanizado en caliente es un método de protección anticorrosiva ampliamente utilizado y muy eficaz para las vigas prefabricadas de acero, especialmente cuando se requiere una durabilidad excepcional o una resistencia superior a la abrasión y al manejo rudo. Este proceso, realizado en plantas especializadas (galvanizadoras), a menudo en colaboración logística con el taller de fabricación de las vigas, implica la inmersión completa de la pieza de acero en un baño de zinc fundido a aproximadamente 450°C.
El Proceso de Galvanizado en Caliente
El galvanizado en caliente no es simplemente un recubrimiento; es un proceso metalúrgico que crea una serie de capas de aleación zinc-hierro intermetálicas sobre el acero, con una capa externa de zinc puro. Estas capas están metalúrgicamente unidas al acero base, proporcionando una adherencia excepcional y una barrera física muy resistente.
El proceso típico de galvanizado en caliente para una viga prefabricada sigue estos pasos fundamentales:
- Desengrase: Eliminación de aceite, grasa y suciedad de la superficie de la viga utilizando una solución alcalina caliente o desengrasantes específicos.
- Enjuague: Lavado con agua para eliminar los residuos de la solución desengrasante.
- Decapado: Inmersión en una solución de ácido clorhídrico o sulfúrico a temperatura ambiente o ligeramente elevada para eliminar el óxido y la calamina de la superficie del acero.
- Enjuague: Nuevo lavado con agua para eliminar los residuos de ácido y las sales de hierro.
- Fluxado: Inmersión en una solución acuosa de cloruro de zinc y cloruro de amonio (flux) a unos 65-80°C. El fluxado elimina los últimos óxidos superficiales, previene la reoxidación del acero antes de la inmersión en zinc y facilita la reacción entre el zinc fundido y el acero.
- Secado (Opcional pero común): Algunas plantas utilizan un horno de secado para eliminar la humedad de la solución de flux antes de la inmersión, evitando salpicaduras peligrosas de zinc fundido.
- Inmersión en Zinc Fundido: La viga se sumerge completamente en el baño de zinc fundido mantenido a unos 445-465°C. El tiempo de inmersión varía según el espesor del acero y el tamaño de la viga, pero suele ser de unos pocos minutos. Durante este tiempo, se forman las capas de aleación zinc-hierro y la capa externa de zinc.
- Extracción y Enfriamiento: La viga se retira lentamente del baño de zinc. El exceso de zinc escurre. Luego, la pieza se enfría, ya sea al aire o mediante inmersión rápida en un tanque de agua o solución de pasivación (quenching). El enfriamiento rápido puede mejorar la apariencia superficial y añadir una protección temporal contra la formación temprana de óxido blanco (manchas de almacenamiento húmedo).
- Inspección y Acabado: Se realiza una inspección visual para verificar la uniformidad, continuidad y adherencia del recubrimiento. Se mide el espesor del recubrimiento de zinc según normas como ISO 1461 o ASTM A123. Se pueden eliminar rebabas o excesos de zinc mediante limado o esmerilado suave si es necesario.
El siguiente resumen detalla las fases clave del proceso de galvanizado en caliente aplicado a vigas de acero.
Etapa del Proceso | Objetivo Principal | Método Común | Importancia |
---|---|---|---|
Desengrase | Eliminar contaminantes orgánicos (aceite, grasa) | Solución alcalina caliente o desengrasante | Asegura la efectividad del decapado posterior. |
Decapado Ácido | Eliminar óxido y calamina | Ácido clorhídrico o sulfúrico | Expone el acero limpio para la reacción con el zinc. |
Fluxado | Limpieza final, prevenir reoxidación, facilitar reacción | Solución de cloruro de zinc y cloruro de amonio | Prepara la superficie para una buena adherencia y formación de capas de aleación. |
Inmersión en Zinc | Formar el recubrimiento protector | Baño de zinc fundido (~450°C) | Creación de las capas de aleación Zn-Fe y la capa externa de Zn puro. |
Enfriamiento / Pasivación | Solidificar el recubrimiento, mejorar apariencia, protección temporal | Aire, agua o solución de pasivación | Controla la estructura final del recubrimiento y previene manchas iniciales. |
Inspección | Verificar calidad y espesor del recubrimiento | Visual, medición de espesores (ISO 1461 / ASTM A123) | Asegura el cumplimiento de especificaciones y la calidad final. |
Ventajas del Galvanizado en Caliente para Vigas Prefabricadas

- Protección Dual: Ofrece protección de barrera (aislando el acero del ambiente) y protección catódica (el zinc se sacrifica para proteger el acero en áreas dañadas).
- Cobertura Completa: Al ser un proceso de inmersión, todas las superficies de la viga (internas y externas), incluyendo bordes, esquinas, huecos y soldaduras, quedan recubiertas de manera uniforme.
- Recubrimiento Resistente: Las capas de aleación intermetálica son muy duras y resistentes a la abrasión y al daño mecánico durante el manejo, transporte y montaje, mucho más que la mayoría de las pinturas.
- Larga Durabilidad: El recubrimiento de galvanizado puede durar décadas sin mantenimiento, incluso en ambientes agresivos. La vida útil es predecible y proporcional al espesor del zinc.
- Inspección Sencilla: La calidad del recubrimiento es fácil de verificar visualmente y mediante medición de espesores. Un recubrimiento que parece continuo y uniforme generalmente lo es.
- Proceso Estandarizado: Normas internacionales como ISO 1461 y ASTM A123 definen claramente los requisitos del proceso y del producto final, asegurando consistencia.
Consideraciones Logísticas y Técnicas para Vigas Grandes en Colombia
El galvanizado en caliente de vigas prefabricadas de gran tamaño o peso presenta desafíos logísticos y técnicos que deben ser gestionados por talleres y galvanizadores experimentados:
- Tamaño de las Cubas de Galvanizado: La limitación principal es el tamaño de los baños de zinc disponibles. En Colombia, existen plantas galvanizadoras con cubas de dimensiones considerables, capaces de manejar vigas de longitudes importantes (por ejemplo, 10, 12 o incluso más metros), pero es crucial verificar la capacidad máxima de la planta seleccionada durante la fase de diseño y planificación. Vigas excepcionalmente largas pueden requerir galvanizado progresivo (doble inmersión) o ser diseñadas en segmentos más cortos.
- Manejo y Peso: Se necesitan grúas y equipos de manejo adecuados tanto en el taller de fabricación como en la planta de galvanizado para manipular las vigas pesadas de forma segura y eficiente.
- Diseño para Galvanizado: Es importante que el diseño de la viga considere los requisitos del proceso de galvanizado. Esto incluye proveer agujeros de ventilación y drenaje adecuados para permitir que el aire y los gases escapen durante la inmersión y que el zinc fundido fluya libremente y drene completamente de todas las cavidades y superficies. Un diseño inadecuado puede causar deformaciones, explosiones de vapor o acumulación excesiva de zinc.
- Composición del Acero: La composición química del acero, especialmente el contenido de silicio y fósforo, puede afectar significativamente la reactividad con el zinc, influenciando el espesor, la apariencia y la estructura del recubrimiento galvanizado (efecto Sandelin). Aceros muy reactivos pueden generar recubrimientos muy gruesos y quebradizos. Es importante conocer y, si es posible, controlar la composición del acero utilizado en las vigas.
- Transporte: La logística de transporte de vigas grandes y pesadas, primero del taller a la planta de galvanizado y luego al sitio de construcción, requiere planificación cuidadosa, permisos especiales si exceden las dimensiones estándar, y equipos de transporte adecuados en Colombia.
Los talleres especializados en Bogotá y otras ciudades industriales de Colombia suelen tener relaciones establecidas con plantas galvanizadoras de confianza y la experiencia necesaria para gestionar estos aspectos, asegurando que incluso vigas de gran tamaño reciban una protección galvanizada de alta calidad.
Monitoreo y Control de Condiciones Ambientales en Taller
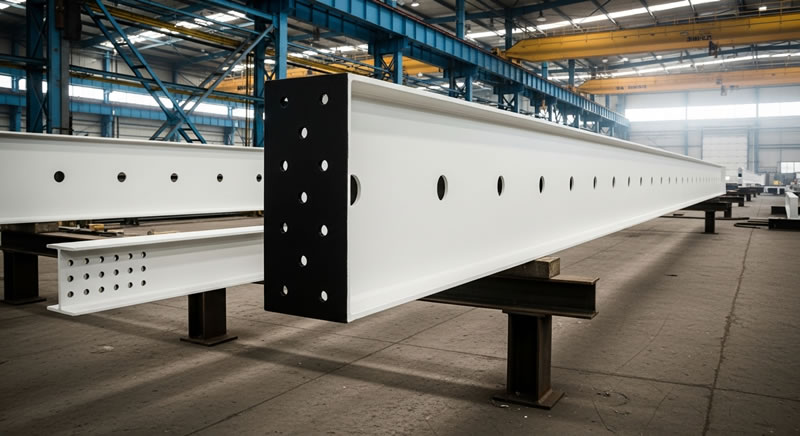
La aplicación exitosa de sistemas de recubrimiento líquido (pinturas) en taller depende críticamente del control de las condiciones ambientales durante las fases de aplicación y curado. Factores como la temperatura (del aire y del sustrato), la humedad relativa (HR) y el punto de rocío son determinantes para la calidad y el desempeño a largo plazo del recubrimiento.
Aplicar recubrimientos fuera de los rangos recomendados por el fabricante puede llevar a una variedad de defectos, incluyendo:
- Mala adherencia.
- Curado incompleto o inadecuado.
- Formación de burbujas, ampollas o porosidad.
- Problemas de apariencia (piel de naranja, corridas, bajo brillo).
- Atrapamiento de solventes.
- Reducción de la vida útil del sistema protector.
Parámetros Críticos y su Control
- Temperatura del Aire y del Sustrato: La mayoría de los recubrimientos tienen rangos de temperatura de aplicación y curado especificados por el fabricante (ej. entre 10°C y 40°C). Temperaturas bajas pueden ralentizar excesivamente el curado (especialmente en epóxicos y poliuretanos) o impedir la correcta formación de la película (en recubrimientos base agua). Temperaturas muy altas pueden acelerar el curado demasiado rápido, causando problemas de aplicación (secado rápido del spray) o atrapamiento de solventes. La temperatura del sustrato (la viga de acero) es particularmente importante y debe medirse directamente. En talleres, se pueden utilizar sistemas de calefacción o ventilación para mantener las temperaturas dentro del rango óptimo.
- Humedad Relativa (HR): La HR es la cantidad de vapor de agua en el aire expresada como porcentaje de la cantidad máxima que podría contener a esa temperatura. Una HR alta (>85% es un límite común) puede retardar la evaporación de solventes, afectar el curado de ciertos recubrimientos (especialmente los sensibles a la humedad como los poliuretanos o los ricos en zinc inorgánico) y aumentar el riesgo de condensación. En talleres, se pueden usar deshumidificadores o sistemas de control de clima para gestionar la HR.
- Punto de Rocío: Es la temperatura a la cual el aire se satura de humedad y comienza a formarse condensación (rocío) sobre una superficie. Es crucial que la temperatura de la superficie de la viga de acero esté siempre por encima del punto de rocío del aire circundante durante la aplicación y el curado inicial. Una regla común es mantener la temperatura del sustrato al menos 3°C (5°F) por encima del punto de rocío. Si la temperatura del sustrato es igual o inferior al punto de rocío, se formará una película invisible de humedad sobre la superficie, lo que impedirá la adherencia del recubrimiento y puede causar corrosión instantánea o ampollamiento posterior.
Monitoreo y Registro
En los talleres que aplican sistemas de protección anticorrosiva de manera profesional, se realiza un monitoreo constante de estas condiciones ambientales utilizando instrumentos calibrados:
- Termómetros: Para medir la temperatura del aire y la temperatura de la superficie del acero (termómetros de contacto o infrarrojos).
- Higrómetros o Psicrómetros: Para medir la humedad relativa del aire.
- Calculadoras de Punto de Rocío: Muchos instrumentos modernos miden T° del aire, HR y T° de superficie, y calculan automáticamente el punto de rocío y el diferencial (T° superficie - Punto de Rocío).
Estos parámetros se miden y registran antes de iniciar la aplicación y periódicamente durante todo el proceso de aplicación y curado. Los registros forman parte integral de la documentación de calidad del proyecto y demuestran que el recubrimiento se aplicó bajo condiciones controladas y conformes a las especificaciones del fabricante y del proyecto. El control ambiental es una de las ventajas clave de la aplicación en taller frente a la aplicación en obra, donde las condiciones climáticas son mucho más variables e impredecibles, especialmente en un país con la diversidad climática de Colombia.
Técnicas Específicas para Zonas Complejas: Bordes y Soldaduras
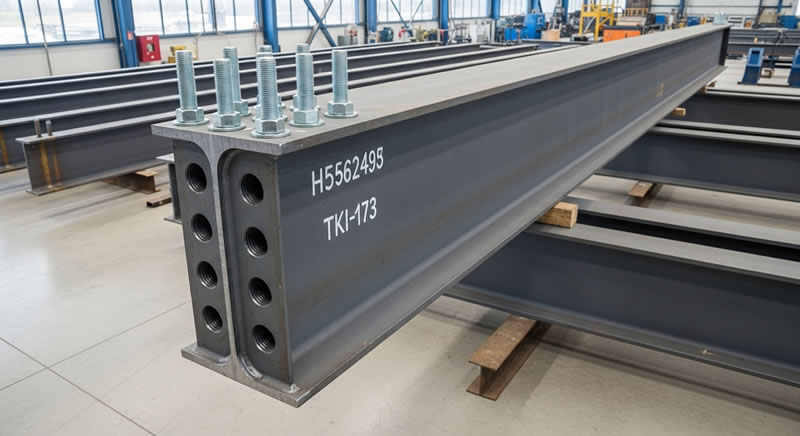
Las vigas prefabricadas, especialmente las armadas o fabricadas, suelen tener geometrías complejas que incluyen bordes afilados, esquinas, cordones de soldadura, conexiones empernadas o soldadas, rigidizadores y otros detalles constructivos. Estas áreas son inherentemente más susceptibles a la corrosión prematura si no se protegen adecuadamente durante la aplicación del sistema anticorrosivo.
Problemática de Bordes y Soldaduras
- Bordes Afilados: Los recubrimientos líquidos tienden a adelgazarse en los bordes afilados debido a la tensión superficial durante la aplicación y el curado ("edge effect"). Esto deja una capa de protección más delgada y vulnerable en estas zonas críticas.
- Cordones de Soldadura: Las soldaduras presentan una superficie irregular, con crestas y valles, que puede ser difícil de cubrir uniformemente. Además, pueden contener escoria residual, salpicaduras de soldadura ("spatter") o porosidad si no se limpian adecuadamente. La zona afectada térmicamente (ZAT) alrededor de la soldadura también puede tener propiedades superficiales diferentes.
- Esquinas Interiores y Zonas de Difícil Acceso: Pueden ser complicadas de alcanzar con los equipos de aplicación (pistolas de spray), resultando en espesores insuficientes o falta de cobertura.
Técnicas de Protección Adicional en Taller
Para asegurar una protección adecuada y uniforme en estas zonas complejas, en el taller se aplican técnicas específicas:
- Preparación de Superficie Cuidadosa: Asegurar que las soldaduras estén limpias, libres de escoria y salpicaduras. Los bordes afilados deben ser suavizados o redondeados mediante esmerilado antes de la preparación de superficie principal (una práctica recomendada es redondear los bordes a un radio mínimo de 2 mm).
- Aplicación de "Stripe Coat" (Capa de Refuerzo): Esta es una práctica fundamental. Consiste en aplicar una capa adicional de imprimación o recubrimiento intermedio manualmente (con brocha o rodillo pequeño) específicamente sobre todos los bordes, esquinas, soldaduras y otras irregularidades antes o después de la aplicación de la capa completa por spray. La aplicación con brocha ayuda a "empujar" el material en las irregularidades y asegura un espesor adecuado en los bordes.
- Técnica de Aplicación por Spray: Utilizar técnicas de pulverización adecuadas, como el "cross-hatching" (pasadas cruzadas perpendiculares), para asegurar una cobertura uniforme. Ajustar la distancia, ángulo y velocidad de la pistola para penetrar en las geometrías complejas.
- Inspección Detallada: Prestar especial atención a estas áreas durante la inspección visual y la medición de espesores de película seca (DFT) para verificar que se ha logrado la cobertura y el espesor requeridos.
- Uso de Recubrimientos Formulados para Bordes: Algunos fabricantes ofrecen recubrimientos (especialmente epóxicos mastic o de altos sólidos) formulados con propiedades reológicas que mejoran la retención en bordes.
La aplicación diligente de estas técnicas en el ambiente controlado del taller es esencial para garantizar que toda la superficie de la viga prefabricada, incluyendo sus puntos más vulnerables, reciba una protección anticorrosiva completa y duradera.
Ensayos Rigurosos de Calidad: Verificación del Sistema Aplicado
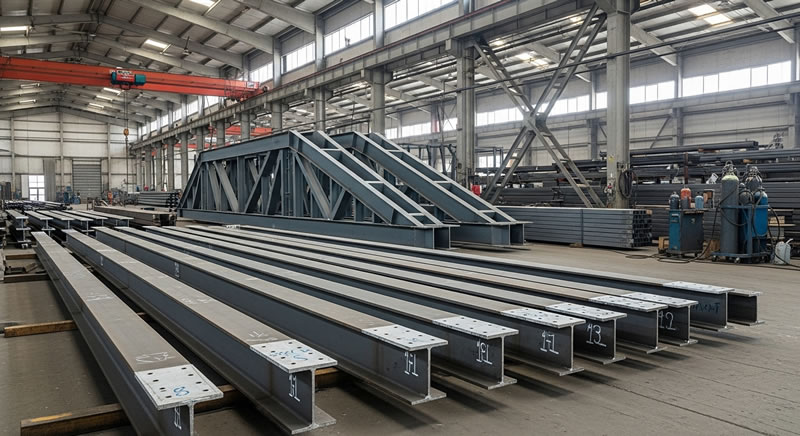
La aplicación de un sistema de protección anticorrosiva en taller no concluye con la última capa de pintura o el enfriamiento tras el galvanizado. Un componente integral del proceso es la realización de una serie de ensayos de calidad para verificar que el sistema aplicado cumple con las especificaciones del proyecto, los estándares de la industria y los requisitos del fabricante del recubrimiento. Estos ensayos aseguran la conformidad del producto final y proporcionan datos objetivos para la documentación de calidad.
Los ensayos clave realizados sobre el sistema de protección aplicado a las vigas prefabricadas en taller incluyen:
Inspección Visual
Es el primer y uno de los controles más importantes. Se realiza después de cada capa y al finalizar el sistema completo. Un inspector cualificado examina visualmente el 100% de las superficies recubiertas buscando defectos como:
- Falta de cobertura (áreas sin pintar o con capa muy fina).
- Corridas o descolgamientos.
- Piel de naranja, cráteres, porosidad.
- Ampollamiento, agrietamiento, delaminación.
- Inclusiones de contaminantes o partículas extrañas.
- Daños mecánicos (rayaduras, abolladuras).
- Uniformidad del color y brillo (para la capa de acabado).
- En galvanizado: áreas no cubiertas, exceso de zinc, rebabas, manchas de ceniza o flux.
Cualquier defecto observado debe ser corregido siguiendo procedimientos aprobados antes de proceder con la siguiente capa o la aceptación final.
Medición de Espesor de Película Seca (DFT - Dry Film Thickness)
Este es uno de los ensayos cuantitativos más críticos. El espesor del recubrimiento está directamente relacionado con la vida útil del sistema de protección. Un espesor insuficiente reduce la protección, mientras que un espesor excesivo puede causar problemas como agrietamiento, mala adherencia entre capas o curado incompleto.
- Equipos: Se utilizan medidores de espesor electrónicos (basados en principios magnéticos o de corrientes de Foucault), debidamente calibrados según estándares como SSPC-PA 2 o ISO 2808.
- Procedimiento: Se toman múltiples lecturas en diferentes puntos de cada viga, siguiendo un patrón estadístico definido en la norma SSPC-PA 2. Esta norma especifica el número de mediciones por área, cómo calcular el promedio por punto y por área, y los criterios de aceptación (usualmente, el promedio por área debe cumplir el mínimo especificado, y ninguna lectura individual puede estar por debajo de un porcentaje del mínimo, ej. 80%).
- Registro: Todos los resultados de DFT se registran meticulosamente como parte del dossier de calidad.
- Para Galvanizado: Se mide el espesor del recubrimiento de zinc utilizando medidores magnéticos, siguiendo los requisitos de ISO 1461 o ASTM A123, que especifican espesores mínimos promedio según el espesor del acero base.
Pruebas de Adherencia
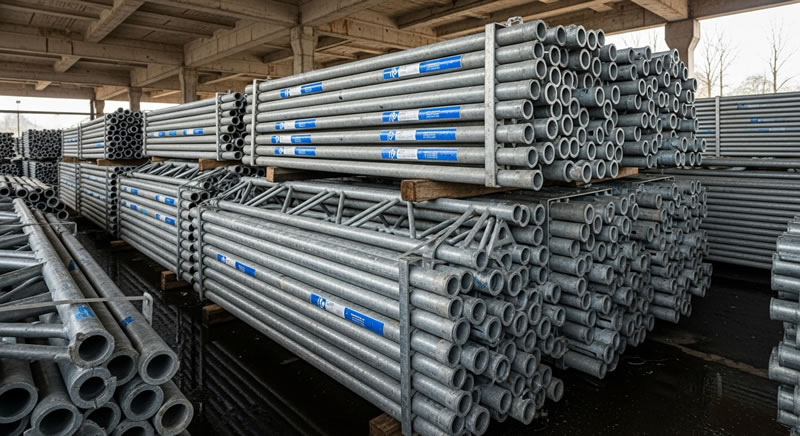
La adherencia mide cuán fuertemente está unido el sistema de recubrimiento al sustrato de acero y entre las diferentes capas. Una buena adherencia es fundamental para el rendimiento a largo plazo.
- Prueba de Corte Cruzado (Cross-Cut Test - ISO 2409 o ASTM D3359 Método B): Se realiza un patrón de cortes en forma de rejilla a través del recubrimiento hasta el sustrato. Luego se aplica una cinta adhesiva estandarizada sobre la rejilla y se retira bruscamente. La cantidad de recubrimiento desprendido se evalúa visualmente comparándola con una escala estándar (0 a 5). Es una prueba cualitativa/semi-cuantitativa, más común para espesores bajos o medios.
- Prueba de Adherencia por Tracción (Pull-Off Test - ISO 4624 o ASTM D4541): Se adhiere un dispositivo de prueba metálico (dolly o sufridera) a la superficie recubierta con un adhesivo adecuado. Una vez curado el adhesivo, se utiliza un equipo de prueba de adherencia portátil que aplica una fuerza de tracción perpendicular a la superficie hasta que el dolly se desprende. Se registra la fuerza necesaria para el desprendimiento (en MPa o psi) y se describe el tipo de fallo (adhesivo entre capas, cohesivo dentro de una capa, fallo en el adhesivo/pegamento, o fallo hasta el sustrato). Esta prueba es cuantitativa y se considera más fiable, especialmente para sistemas de alto rendimiento y mayor espesor. Se especifica un valor mínimo de adherencia requerido (ej. 5 MPa).
Las pruebas de adherencia suelen realizarse en puntos representativos o según lo especificado en el plan de calidad del proyecto.
Detección de Discontinuidades (Holiday Detection)
Este ensayo se utiliza para localizar pequeños defectos o discontinuidades en el recubrimiento (pinholes, poros, áreas de bajo espesor) que no son fácilmente visibles pero que pueden permitir el paso de humedad y electrolitos hasta el sustrato, iniciando la corrosión. Es especialmente importante para recubrimientos de barrera destinados a servicio en inmersión o ambientes muy agresivos.
- Equipos: Se utilizan detectores de "holidays" de bajo voltaje (tipo esponja húmeda, para DFT < 500 µm) o de alto voltaje (tipo chispa eléctrica, para DFT > 500 µm), según ISO 29601 o NACE SP0188.
- Procedimiento: Se pasa una sonda (esponja húmeda o electrodo) sobre toda la superficie recubierta. Una señal audible o visual indica la presencia de una discontinuidad cuando se completa un circuito eléctrico a través del defecto hasta el sustrato.
- Reparación: Todas las discontinuidades detectadas deben ser marcadas y reparadas siguiendo procedimientos aprobados.
La siguiente tabla resume los principales ensayos de calidad realizados en taller sobre los sistemas anticorrosivos aplicados a vigas prefabricadas.
Ensayo de Calidad | Propósito Principal | Método/Estándar Común | Parámetro Medido/Evaluado | Importancia |
---|---|---|---|---|
Inspección Visual | Detectar defectos superficiales y de aplicación | Observación directa, comparación con estándares visuales | Apariencia, uniformidad, presencia de defectos (corridas, poros, etc.) | Control básico y esencial de la calidad de aplicación. |
Medición de Espesor de Película Seca (DFT) | Verificar que el espesor cumple especificaciones | Medidores magnéticos/electrónicos (SSPC-PA 2, ISO 2808) | Espesor del recubrimiento en micrones (µm) o mils | El espesor es crítico para la durabilidad y el rendimiento protector. |
Prueba de Adherencia (Corte Cruzado) | Evaluar cualitativamente la adherencia | ISO 2409, ASTM D3359-B | Cantidad de recubrimiento desprendido (Escala 0-5) | Indicador rápido de problemas de adherencia, útil para capas finas. |
Prueba de Adherencia (Tracción Pull-Off) | Medir cuantitativamente la fuerza de adherencia | ISO 4624, ASTM D4541 | Fuerza de desprendimiento (MPa o psi), tipo de fallo | Medida objetiva de la adherencia, requerida para sistemas de alto rendimiento. |
Detección de Discontinuidades (Holiday Test) | Localizar defectos tipo poro o "pinhole" | Detectores bajo/alto voltaje (ISO 29601, NACE SP0188) | Presencia/ausencia de discontinuidades | Esencial para asegurar la integridad de la barrera en ambientes severos o inmersión. |
Verificación del Curado | Asegurar que el recubrimiento ha curado adecuadamente | Pruebas de dureza (lápiz, péndulo), resistencia al solvente (MEK rub test - ASTM D4752) | Dureza, resistencia al ablandamiento por solvente | Un curado incompleto compromete las propiedades protectoras y mecánicas. |
La realización sistemática de estos ensayos en el taller proporciona una garantía de calidad mucho mayor que la que se podría lograr con aplicaciones realizadas en obra bajo condiciones menos controladas.
Capacidad para Ambientes de Alta Agresividad Corrosiva (C4, C5)
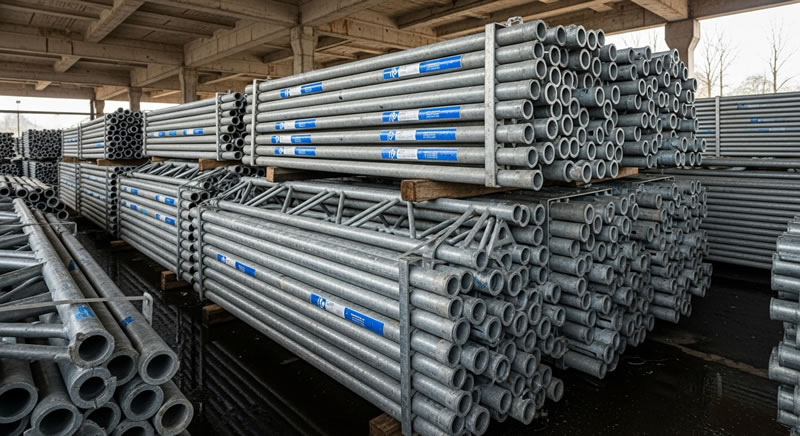
Las estructuras metálicas en Colombia pueden estar expuestas a una amplia variedad de ambientes, desde los relativamente benignos C1 (interiores secos) hasta los extremadamente agresivos C5 (industriales con alta humedad y atmósferas agresivas, o zonas costeras/marinas con alta salinidad). Las vigas prefabricadas pueden ser destinadas a proyectos en cualquiera de estas condiciones, por lo que es fundamental que el taller de aplicación de la protección anticorrosiva esté equipado y tenga la experiencia necesaria para aplicar sistemas diseñados para los ambientes más severos (C4 - Alta, y C5 - Muy Alta).
La norma ISO 12944-2 clasifica los ambientes atmosféricos según su corrosividad:
- C1 (Muy Baja): Interiores de edificios con calefacción y atmósfera limpia (oficinas, tiendas).
- C2 (Baja): Exteriores con baja contaminación (atmósferas rurales) o interiores sin calefacción donde puede haber condensación (almacenes, polideportivos).
- C3 (Media): Exteriores urbanos e industriales con contaminación moderada de dióxido de azufre, o zonas costeras de baja salinidad. Interiores con alta humedad y algo de contaminación (plantas de alimentos, lavanderías).
- C4 (Alta): Exteriores industriales y zonas costeras con salinidad moderada. Interiores de plantas químicas, piscinas, astilleros. Bogotá, debido a su tráfico e industria, puede tener zonas que se aproximen a C3 o incluso C4 en microclimas específicos.
- C5 (Muy Alta): Exteriores industriales con alta humedad y atmósfera agresiva, y zonas costeras/marinas con alta salinidad. Interiores con condensación casi permanente y alta contaminación. Las zonas costeras de Colombia (Caribe y Pacífico) y áreas industriales pesadas caen típicamente en esta categoría.
La protección de vigas prefabricadas para ambientes C4 y C5 requiere:
- Preparación de Superficie de Alto Nivel: Generalmente se exige un grado Sa 2½ (SSPC-SP 10) o incluso Sa 3 (SSPC-SP 5).
- Sistemas de Recubrimiento Robustos: Se especifican sistemas multicapa de alto rendimiento, típicamente basados en imprimaciones ricas en zinc (inorgánico u orgánico), seguidas de una o dos capas intermedias epóxicas de alto espesor, y un acabado resistente a la intemperie (poliuretano alifático o polisiloxano). Los espesores totales de película seca (DFT) suelen ser elevados (superiores a 250-300 µm).
- Alternativa de Galvanizado: El galvanizado en caliente (posiblemente seguido de un sistema dúplex - pintura sobre galvanizado) es una opción muy duradera y frecuentemente considerada para ambientes C4 y C5, ofreciendo una excelente protección contra la corrosión y la abrasión.
- Control de Calidad Estricto: Todos los pasos del proceso (preparación, condiciones ambientales, aplicación, ensayos) deben ser rigurosamente controlados y documentados. La detección de discontinuidades suele ser obligatoria.
- Experiencia y Equipamiento: El taller debe contar con personal capacitado, equipos de aplicación adecuados (ej. airless de alta presión) y un sistema de gestión de calidad robusto para manejar estos sistemas exigentes.
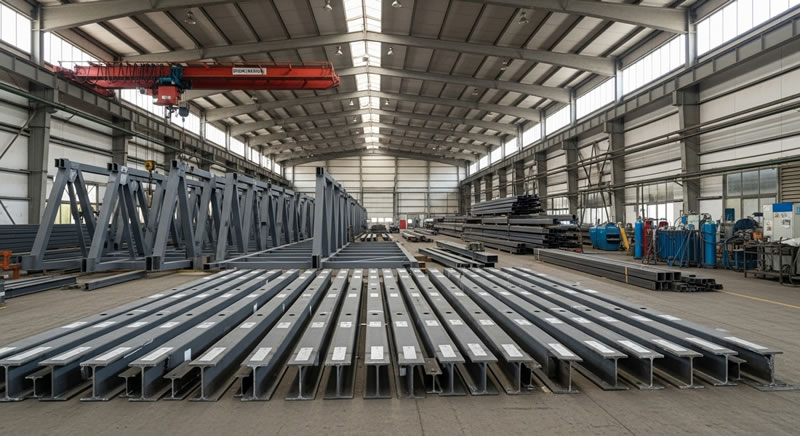
Los talleres especializados en estructuras metálicas y protección anticorrosiva en Colombia están generalmente preparados para afrontar estos retos, ofreciendo soluciones certificadas y garantizadas para las condiciones ambientales más agresivas del país, asegurando la longevidad de las vigas prefabricadas en proyectos críticos.
La siguiente tabla ilustra ejemplos de sistemas de protección típicos recomendados por ISO 12944-5 para diferentes categorías de corrosividad y durabilidades esperadas (L, M, H - Baja, Media, Alta), aplicables a vigas de acero.
Categoría Corrosividad | Durabilidad Esperada | Ejemplo Sistema (ISO 12944-5) | Preparación Superficie | DFT Total Típico (µm) |
---|---|---|---|---|
C2 (Baja) | Media (M: 5-15 años) | Alquídico (Imprimación + Acabado) | Sa 2 / St 3 | 80 - 120 |
C3 (Media) | Alta (H: >15 años) | Epoxi (Impr.) + Poliuretano (Acab.) | Sa 2½ | 160 - 240 |
C4 (Alta) | Alta (H: >15 años) | Epoxi Rico Zinc (Impr.) + Epoxi (Int.) + Poliuretano (Acab.) | Sa 2½ | 240 - 320 |
C4 (Alta) | Muy Alta (VH: >25 años) | Galvanizado en caliente (según ISO 1461, ej. 85µm) | Decapado químico | ≥ 85 (Zn) |
C5 (Muy Alta) | Alta (H: >15 años) | Epoxi Rico Zinc Inorg. (Impr.) + Epoxi (Int.) + Poliuretano (Acab.) | Sa 2½ / Sa 3 | 300 - 500+ |
C5 (Muy Alta) | Alta (H: >15 años) | Galvanizado en caliente + Sistema Dúplex (Epoxi + Poliuretano) | Decapado + Barrido ligero (si aplica) | Zn + 160-240 (pintura) |
Ventajas Decisivas de la Aplicación en Taller frente a la Aplicación en Obra

La decisión de aplicar los sistemas de protección anticorrosiva a las vigas prefabricadas en un taller especializado en lugar de hacerlo en el sitio de construcción ofrece una serie de ventajas significativas que impactan positivamente en la calidad final, la durabilidad de la estructura, los costos del proyecto y los plazos de ejecución.
Control de Calidad Superior
- Condiciones Ambientales Controladas: Como se discutió anteriormente, el taller permite un control preciso de la temperatura, humedad y punto de rocío, factores críticos para la correcta aplicación y curado de los recubrimientos. Esto elimina las incertidumbres asociadas al clima variable en obra (lluvia, viento, sol directo, temperaturas extremas), especialmente relevante en la geografía diversa de Colombia.
- Preparación de Superficie Óptima: Los equipos de chorreado abrasivo confinados en cabinas dentro del taller permiten alcanzar y verificar consistentemente los grados de limpieza y perfiles de anclaje requeridos (Sa 2½, Sa 3), algo mucho más difícil y costoso de lograr en campo. Además, se facilita la contención y gestión de los residuos del chorreado.
- Aplicación Uniforme: El uso de equipos de aplicación especializados (pistolas airless, sistemas electrostáticos si aplica), la buena iluminación y la accesibilidad a todas las caras de la viga en el taller favorecen la obtención de espesores de película uniformes y la correcta cobertura de zonas complejas.
- Inspección Rigurosa: La inspección y los ensayos de calidad (DFT, adherencia, detección de discontinuidades) se pueden realizar de manera más sistemática, exhaustiva y bajo condiciones adecuadas en el taller por personal especializado.
Mayor Durabilidad y Rendimiento del Sistema Protector
- Adherencia Mejorada: La preparación de superficie superior y la aplicación bajo condiciones controladas resultan en una mejor adherencia del sistema de recubrimiento al sustrato de acero, lo cual es fundamental para la durabilidad a largo plazo.
- Menor Riesgo de Defectos: Al minimizar la influencia de factores ambientales adversos y asegurar una aplicación experta, se reduce significativamente la probabilidad de defectos en el recubrimiento (porosidad, ampollamiento, curado incompleto) que podrían llevar a fallos prematuros.
- Cumplimiento de Especificaciones: Es más probable que el sistema aplicado en taller cumpla consistentemente con todos los requisitos de las especificaciones del proyecto y las recomendaciones del fabricante del recubrimiento, asegurando el rendimiento esperado.
Eficiencia en Tiempos y Costos del Proyecto
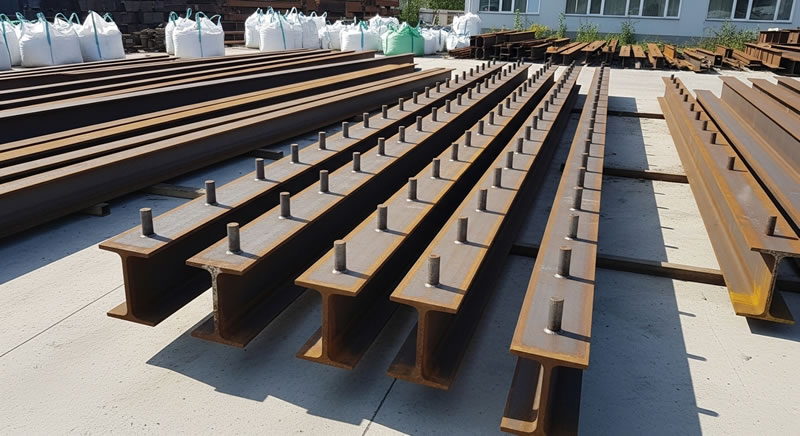
- Optimización del Cronograma: La protección de las vigas puede realizarse en paralelo con otras actividades de la obra (cimentaciones, preparación del sitio), desacoplando esta tarea crítica del cronograma principal de montaje. Las vigas llegan a obra listas para ser instaladas, acelerando el proceso constructivo.
- Mayor Productividad: El entorno de taller permite una mayor eficiencia en la aplicación (líneas de producción, equipos fijos, personal especializado) comparado con las condiciones a menudo congestionadas y menos organizadas de una obra.
- Reducción de Costos Indirectos: Se evitan los costos asociados a la movilización de equipos de preparación y aplicación a la obra, la construcción de andamios o plataformas de trabajo específicas para pintar en altura, la protección de áreas adyacentes contra el overspray, y las posibles demoras por mal tiempo.
- Menor Impacto Ambiental en Obra: Se reduce la generación de polvo, ruido y residuos peligrosos (solventes, restos de pintura) en el sitio de construcción. La gestión de estos aspectos es más controlada y eficiente en un taller preparado.
Seguridad Mejorada
- Menor Exposición a Riesgos en Obra: Se reduce la necesidad de trabajos de pintura en altura o en condiciones potencialmente peligrosas en el sitio de construcción.
- Control de Riesgos Laborales: Los talleres cuentan con instalaciones diseñadas para manejar los riesgos asociados a la preparación de superficie (polvo, ruido) y la aplicación de recubrimientos (vapores de solventes, inflamabilidad), con sistemas de ventilación, extracción y equipos de protección personal adecuados.
A continuación, se presenta una comparación directa entre la aplicación de sistemas anticorrosivos en taller versus en obra para vigas prefabricadas.
Factor | Aplicación en Taller | Aplicación en Obra |
---|---|---|
Control de Condiciones Ambientales (T°, HR, Punto Rocío) | Alto control, predecible. | Bajo control, dependiente del clima, impredecible. |
Calidad de Preparación de Superficie | Óptima y consistente (Sa 2½, Sa 3 fácil de lograr). Contención de residuos. | Difícil de lograr consistentemente altos grados. Problemas de contención. Mayor costo. |
Calidad y Uniformidad de Aplicación | Alta, facilitada por equipos, iluminación y accesibilidad. | Variable, afectada por acceso, viento, condiciones. Mayor riesgo de defectos. |
Control de Calidad y Ensayos | Sistemático, riguroso, fácil de implementar. | Más complejo, acceso limitado, condiciones variables. |
Durabilidad Esperada del Sistema | Máxima posible según el sistema especificado. | Potencialmente reducida debido a condiciones subóptimas. |
Eficiencia y Productividad | Alta, proceso optimizado. | Baja, interferencias, condiciones variables. |
Impacto en Cronograma de Obra | Positivo, acelera el montaje al llegar las piezas listas. | Negativo, actividad en ruta crítica, sensible a demoras climáticas. |
Costos (Directos e Indirectos) | Generalmente más eficiente en costo total del ciclo de vida. | Puede parecer más barato inicialmente, pero mayores costos indirectos, de retoques y menor durabilidad. |
Seguridad Laboral | Mayor control de riesgos en entorno industrial. | Mayores riesgos (trabajo en altura, condiciones de obra). |
Impacto Ambiental en Sitio | Mínimo. | Mayor (polvo, ruido, residuos, VOCs). |
Si bien la aplicación en taller requiere una planificación logística cuidadosa para el transporte de las vigas protegidas, las ventajas en términos de calidad, durabilidad y eficiencia global del proyecto suelen ser preponderantes, especialmente para sistemas de protección de alto rendimiento y proyectos con altos estándares de calidad, como los que se acometen frecuentemente en Bogotá y otras regiones clave de Colombia.
Procedimientos Cuidadosos de Embalaje, Manipulación y Transporte
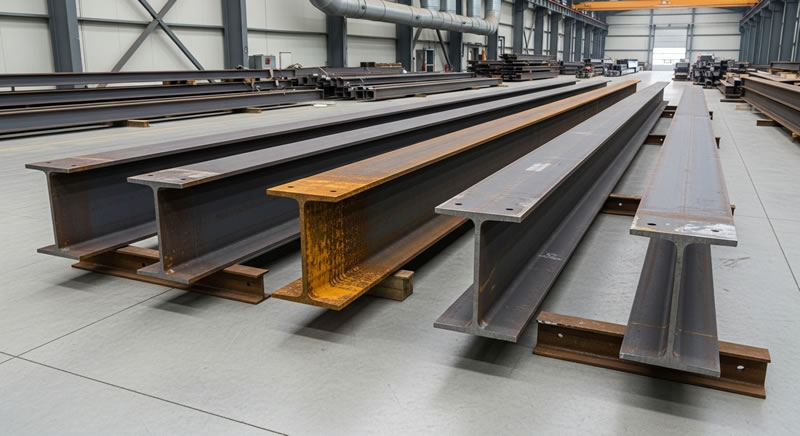
Una vez que el sistema de protección anticorrosiva ha sido aplicado, curado e inspeccionado satisfactoriamente en el taller, es crucial implementar procedimientos adecuados para el embalaje, la manipulación y el transporte de las vigas prefabricadas hasta el sitio de construcción. El objetivo es preservar la integridad del recubrimiento o galvanizado, evitando daños mecánicos (rayaduras, golpes, abrasión) que podrían comprometer la protección y requerir costosas reparaciones en obra.
Embalaje y Protección
- Tiempo de Curado Adecuado: Asegurarse de que el recubrimiento esté completamente curado según las especificaciones del fabricante antes de proceder al embalaje o apilamiento. Un curado insuficiente puede hacer que el recubrimiento sea susceptible a daños por presión o adherencia entre piezas.
- Materiales de Separación y Amortiguación: Utilizar materiales blandos y no abrasivos como separadores entre las vigas apiladas o agrupadas. Esto puede incluir bloques de madera blanda, caucho, poliestireno expandido o fieltros protectores. Los puntos de contacto deben ser minimizados y ubicados estratégicamente para distribuir el peso y evitar la concentración de esfuerzos sobre el recubrimiento.
- Protección de Bordes y Esquinas: Las zonas más vulnerables a daños, como bordes y esquinas, pueden requerir protección adicional mediante cantoneras de plástico, cartón grueso o envolturas específicas.
- Agrupación y Sujeción: Las vigas pueden agruparse utilizando flejes de plástico o textiles (evitando flejes metálicos directamente sobre el recubrimiento) o sistemas de embalaje específicos, asegurando que la sujeción no dañe la pintura.
- Identificación Clara: Cada viga o paquete debe estar claramente identificado con la información relevante del proyecto (número de pieza, contrato, destino) para facilitar la logística y el montaje en obra.
Manipulación (Carga y Descarga)

- Equipos Adecuados: Utilizar grúas, montacargas u otros equipos de elevación con la capacidad adecuada para el peso y las dimensiones de las vigas.
- Eslingas y Accesorios de Izaje: Emplear eslingas anchas de material textil (nylon, poliéster) o estrobos protegidos para evitar el contacto directo de cadenas o cables de acero con la superficie recubierta. Los puntos de izaje deben ser seleccionados cuidadosamente para equilibrar la carga y minimizar la presión sobre el recubrimiento. Se pueden usar balancines o vigas separadoras para cargas largas.
- Personal Capacitado: La manipulación debe ser realizada por personal experimentado y consciente de la necesidad de proteger el recubrimiento. Evitar arrastrar las vigas por el suelo o permitir impactos bruscos.
- Superficies de Apoyo: Asegurar que las áreas donde se apoyarán temporalmente las vigas (en el taller, en el transporte, en la obra) estén limpias, niveladas y protegidas con durmientes o soportes adecuados para evitar contaminación o daños.
Transporte
- Vehículos Apropiados: Utilizar camiones o plataformas de transporte adecuados para las dimensiones y el peso de las vigas, asegurando que la carga esté estable y bien distribuida.
- Sujeción Segura: La carga debe ser asegurada firmemente al vehículo utilizando cadenas o cinchas, pero siempre interponiendo elementos de protección (madera, caucho, protectores de esquina) entre los dispositivos de sujeción y la superficie recubierta para prevenir daños por abrasión o presión excesiva durante el tránsito.
- Planificación de Ruta: Para vigas de gran tamaño, planificar la ruta de transporte considerando posibles restricciones de altura, anchura o peso, especialmente en trayectos largos dentro de Colombia o en accesos a zonas urbanas como Bogotá. Obtener los permisos necesarios si se trata de cargas extradimensionadas.
- Inspección a la Llegada: Al recibir las vigas en obra, realizar una inspección para verificar si se han producido daños durante el transporte y documentar cualquier incidencia.
La implementación rigurosa de estos procedimientos de embalaje, manipulación y transporte es el último paso crítico en el proceso de aplicación en taller para asegurar que las vigas prefabricadas lleguen a su destino final con el sistema de protección anticorrosiva intacto y listo para proporcionar la durabilidad esperada.
Documentación Exhaustiva del Proceso: El Dossier de Calidad
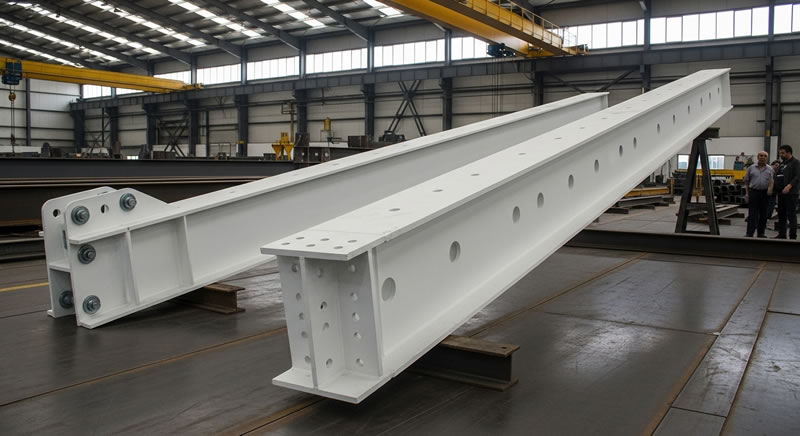
Un aspecto fundamental que diferencia la aplicación profesional de sistemas anticorrosivos en taller es la generación de una documentación completa y trazable de todo el proceso. Esta documentación se compila en lo que se conoce como el Dossier de Calidad o Informe Final de Protección Anticorrosiva, y sirve como evidencia objetiva del cumplimiento de las especificaciones y estándares de calidad.
El Dossier de Calidad típicamente incluye, como mínimo, la siguiente información para cada lote o conjunto de vigas prefabricadas procesadas:
- Identificación del Proyecto y las Piezas: Nombre del proyecto, cliente, números de contrato, listado e identificación única de las vigas incluidas en el informe.
- Especificaciones Aplicables: Referencia a las normas (ISO, SSPC, ASTM, normativas colombianas como la NSR-10 si aplica), especificaciones del proyecto y hojas técnicas de los productos utilizados.
- Registros de Preparación de Superficie:
- Método utilizado (ej. chorreado abrasivo).
- Tipo y tamaño del abrasivo.
- Grado de limpieza alcanzado (ej. Sa 2½ según ISO 8501-1) y evidencia de verificación (comparadores visuales).
- Mediciones del perfil de anclaje (método y resultados, ej. 50-75 µm según ASTM D4417-C).
- Resultados de pruebas de contaminación por sales (ej. cloruros < 20 mg/m² según ISO 8502-9).
- Fecha y hora de la preparación.
- Registros de Condiciones Ambientales:
- Temperaturas del aire, del sustrato y punto de rocío medidas antes y durante la aplicación de cada capa.
- Humedad relativa.
- Verificación de que las condiciones estuvieron dentro de los rangos permitidos (ej. T° sustrato > Punto de Rocío + 3°C, HR < 85%).
- Equipo utilizado para las mediciones y su calibración.
- Registros de Aplicación de Recubrimientos / Galvanizado:
- Identificación de los productos aplicados (nombre, fabricante, número de lote) para cada capa (imprimación, intermedia, acabado).
- Método de aplicación (ej. spray airless, brocha para stripe coat).
- Relación de mezcla (para productos de dos componentes).
- Dilución utilizada (si aplica).
- Fecha y hora de aplicación de cada capa.
- Para galvanizado: parámetros del proceso (tiempos, temperaturas), norma aplicada (ISO 1461).
- Registros de Inspección y Ensayos de Calidad:
- Resultados de la inspección visual (descripción de conformidad o defectos encontrados y corregidos).
- Resultados detallados de la medición de Espesor de Película Seca (DFT), incluyendo ubicación de las mediciones, lecturas individuales, promedios y cumplimiento de SSPC-PA 2.
- Resultados de las pruebas de adherencia (método, ubicación, resultados cuantitativos o cualitativos, tipo de fallo).
- Resultados de la detección de discontinuidades (si aplica) y registro de reparaciones.
- Resultados de pruebas de curado (si aplican).
- Certificados de calibración de los equipos de medición e inspección utilizados.
- Información del Aplicador y del Inspector: Nombres y cualificaciones del personal responsable de la aplicación y de la inspección/control de calidad.
- Declaración de Conformidad: Una declaración final firmada por el responsable de calidad del taller, confirmando que el trabajo se realizó de acuerdo con las especificaciones y estándares requeridos.
Este Dossier de Calidad no solo proporciona una garantía al cliente y al propietario del proyecto, sino que también es una herramienta valiosa para la gestión de la calidad interna del taller, para la trazabilidad en caso de futuros mantenimientos o problemas, y como registro histórico del desempeño del sistema de protección. La capacidad de generar esta documentación detallada y fiable es una característica distintiva de los procesos de aplicación de protección anticorrosiva realizados en un entorno de taller profesional y bien gestionado.
Sinergia entre Taller de Fabricación y Planta de Galvanizado: Logística Clave en Colombia
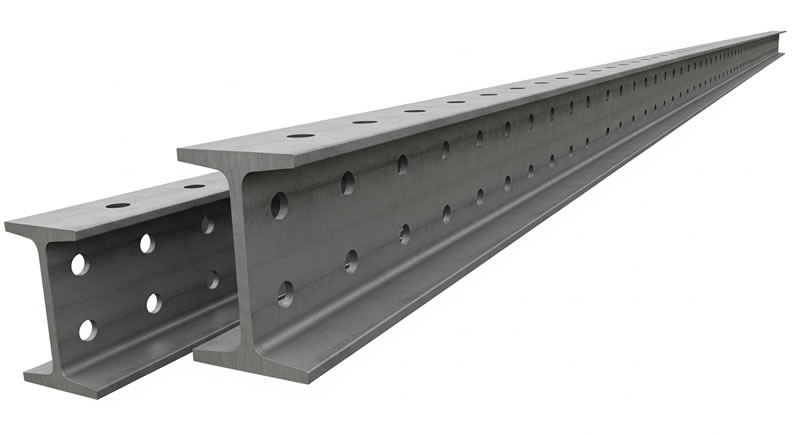
Cuando se especifica el galvanizado en caliente como sistema de protección para las vigas prefabricadas, la coordinación logística y técnica entre el taller donde se fabrican las vigas y la planta de galvanizado es un factor crítico para el éxito del proceso. Esta colaboración es especialmente relevante en el contexto colombiano, donde las distancias entre los centros de fabricación (como Bogotá o Medellín) y las plantas de galvanizado con capacidad para piezas grandes pueden ser significativas.
Los aspectos clave de esta sinergia incluyen:
- Comunicación Temprana en Diseño: Es fundamental que el diseñador estructural y el taller de fabricación consideren los requisitos del galvanizado desde las etapas iniciales del diseño de las vigas. Esto implica consultar con la planta galvanizadora para confirmar la capacidad de sus cubas, discutir la necesidad y ubicación de agujeros de ventilación y drenaje, y considerar la composición química del acero si es posible. Una comunicación fluida evita problemas como deformaciones, piezas que no caben en la cuba o recubrimientos de mala calidad.
- Planificación Logística del Transporte: Se debe coordinar el transporte eficiente y seguro de las vigas fabricadas desde el taller hasta la planta de galvanizado, y posteriormente desde la planta de galvanizado hasta el sitio de construcción (o de vuelta al taller si se requiere algún acabado adicional, como un sistema dúplex). Esto implica seleccionar transportistas adecuados, optimizar rutas y obtener permisos si es necesario, considerando la infraestructura vial de Colombia.
- Programación Conjunta: Alinear los cronogramas de producción del taller con la disponibilidad y capacidad de procesamiento de la planta galvanizadora para evitar cuellos de botella y asegurar que las vigas estén listas según el cronograma general del proyecto.
- Intercambio de Información Técnica: El taller debe proporcionar a la planta galvanizadora información clara sobre las piezas (identificación, dimensiones, pesos, tipo de acero) y cualquier requisito especial. A su vez, la planta galvanizadora debe informar sobre sus procedimientos estándar, limitaciones y cualquier observación relevante durante el proceso.
- Inspección Coordinada: Definir los puntos de inspección y criterios de aceptación tanto en el taller (antes del envío a galvanizar) como en la planta galvanizadora (después del proceso). A menudo, inspectores del taller o del cliente pueden presenciar el proceso o realizar inspecciones en la planta galvanizadora.
- Manejo de No Conformidades: Establecer un procedimiento claro para manejar cualquier no conformidad detectada durante el galvanizado (áreas sin cubrir, deformaciones, etc.), incluyendo la comunicación rápida y la definición de acciones correctivas (reparación según ISO 1461, reprocesamiento, etc.).
Una relación sólida y colaborativa entre el fabricante de las vigas y el galvanizador, basada en la experiencia y la confianza mutua, es esencial para garantizar que las vigas prefabricadas galvanizadas cumplan con los más altos estándares de calidad y lleguen a tiempo a la obra.
Selección del Sistema Anticorrosivo: Adaptación al Contexto Colombiano
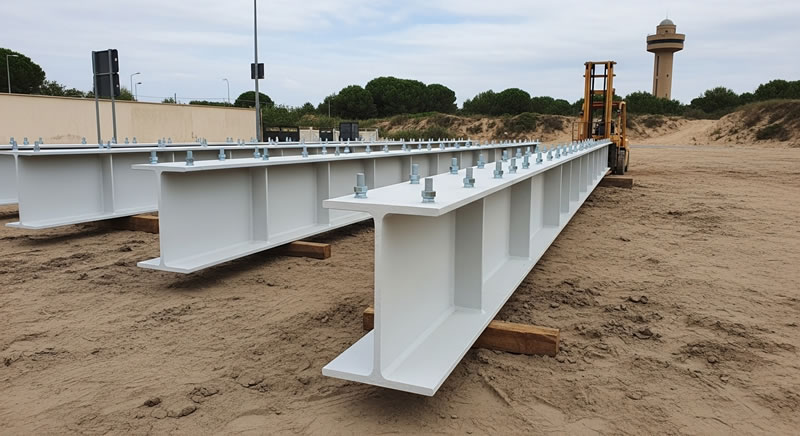
Si bien los principios de protección anticorrosiva y los estándares internacionales son universalmente aplicables, la selección óptima del sistema para vigas prefabricadas en Colombia debe considerar las particularidades del país:
- Diversidad Climática: Colombia presenta una gran variedad de microclimas, desde las zonas andinas relativamente secas y templadas (como Bogotá, aunque con alta humedad relativa nocturna y contaminación urbana) hasta las regiones costeras cálidas y muy húmedas con alta salinidad (Caribe y Pacífico), pasando por zonas de selva tropical con lluvias intensas y alta humedad constante. La categoría de corrosividad (C1 a C5) puede variar significativamente en distancias cortas. Es crucial una evaluación precisa del ambiente específico donde se ubicará la estructura.
- Contaminación Industrial y Urbana: Las principales ciudades como Bogotá, Medellín y Cali, así como los corredores industriales, presentan niveles de contaminación atmosférica (SOx, NOx, partículas) que pueden acelerar la corrosión, empujando la clasificación ambiental hacia C3 o C4 en ciertas áreas.
- Disponibilidad de Tecnologías y Materiales: Aunque Colombia cuenta con una industria de pinturas y recubrimientos desarrollada y plantas de galvanizado modernas, la disponibilidad de ciertas tecnologías muy especializadas o productos importados puede variar. Es importante seleccionar sistemas que utilicen materiales y tecnologías probadas y disponibles localmente, con soporte técnico adecuado.
- Normativa Local: El Reglamento Colombiano de Construcción Sismo Resistente (NSR-10), en su Título F sobre estructuras metálicas, establece requisitos generales de durabilidad y protección contra la corrosión, haciendo referencia a estándares internacionales pero enfatizando la necesidad de adaptación a las condiciones locales. Para sistemas intumescentes de protección contra fuego, se deben cumplir los requisitos específicos de resistencia al fuego definidos en el Título J y K de la NSR-10.
- Prácticas Constructivas y Mano de Obra: Considerar las prácticas habituales de montaje y la disponibilidad de mano de obra calificada para realizar eventuales retoques o reparaciones menores en obra, aunque el objetivo principal de la aplicación en taller es minimizar esta necesidad.
Por lo tanto, la especificación del sistema anticorrosivo para vigas prefabricadas en Colombia no debe ser una simple copia de estándares extranjeros, sino el resultado de un análisis que considere el ambiente específico, la vida útil requerida, la normativa local, la disponibilidad de soluciones y la experiencia de los aplicadores y fabricantes locales. La colaboración con talleres y proveedores con experiencia comprobada en el mercado colombiano es valiosa para tomar la decisión más adecuada y costo-efectiva a largo plazo.
La Importancia de la Protección Integral en Taller
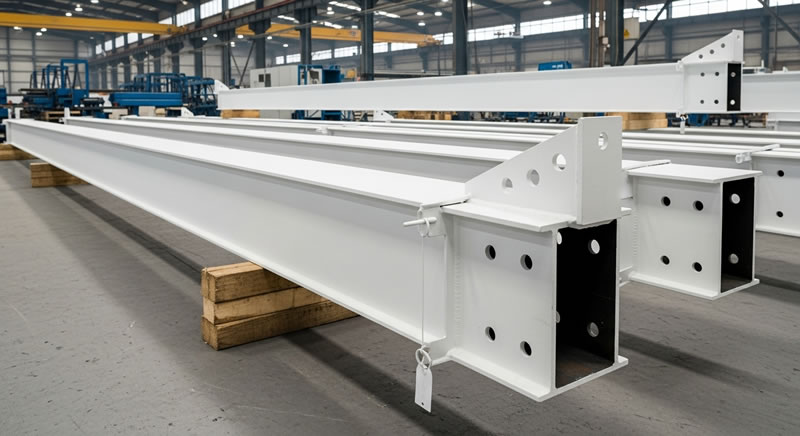
La aplicación de sistemas de protección anticorrosiva en taller para vigas prefabricadas de acero representa un enfoque integral que va más allá de la simple aplicación de pintura o zinc. Es un proceso controlado, documentado y basado en la ingeniería, que busca maximizar la vida útil de las estructuras metálicas, asegurar la seguridad y optimizar los recursos del proyecto. Desde la meticulosa preparación de la superficie, pasando por la selección y aplicación experta del sistema adecuado (sea pintura de alto rendimiento o galvanizado), hasta el control riguroso de calidad y la gestión cuidadosa del manejo y transporte, cada etapa contribuye a entregar un componente estructural de alta calidad.
Las vigas metálicas armadas o fabricadas, y en particular las prefabricadas, son elementos cruciales en innumerables proyectos de construcción en Bogotá y toda Colombia, desde edificaciones y puentes hasta instalaciones industriales y comerciales. Asegurar su protección contra la corrosión desde la fase de fabricación en taller no es un gasto, sino una inversión fundamental en la durabilidad, seguridad y sostenibilidad de la infraestructura del país. Los talleres especializados que dominan estas técnicas ofrecen una garantía de calidad y rendimiento que difícilmente puede ser igualada por las aplicaciones realizadas bajo las condiciones variables e impredecibles de la obra.