Desarrollo de Prototipos y Ejecución de Ensayos Específicos para Vigas Metálicas Personalizadas a Medida Destinadas a Proyectos Especiales en Acero: Validación, Verificación y Optimización en el Contexto de las Vigas Armadas o Fabricadas en Colombia.
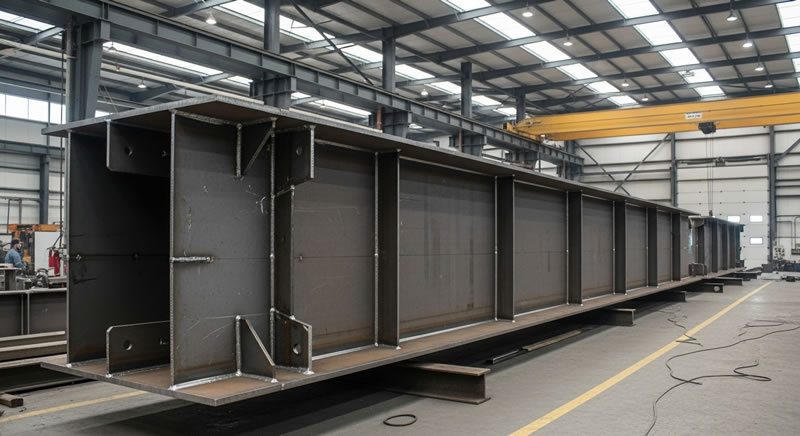
La ingeniería de estructuras metálicas, particularmente en el ámbito de las vigas de acero armadas o fabricadas, alcanza un nivel superior de complejidad y exigencia cuando se abordan proyectos especiales que demandan soluciones a medida. Las vigas personalizadas no son elementos estandarizados; son el resultado de un diseño específico para cumplir requisitos únicos de carga, geometría, funcionalidad o estética. En este escenario, la confianza absoluta en el desempeño estructural es primordial. Si bien los análisis computacionales avanzados, como el Método de Elementos Finitos (FEA), proporcionan predicciones valiosas, existen situaciones donde la singularidad del diseño, la criticidad de la aplicación o la ausencia de precedentes comparables justifican un paso adicional de validación física: el desarrollo de prototipos y la ejecución de ensayos específicos.
Esta fase, aunque identificada como "si es necesario", representa una herramienta poderosa dentro del arsenal del ingeniero estructural y del fabricante especializado. No se trata de una rutina aplicable a toda viga personalizada, sino de una decisión estratégica basada en una evaluación rigurosa de los riesgos y las incertidumbres inherentes al proyecto. Optar por el prototipado y los ensayos es una inversión en seguridad, fiabilidad y optimización, que busca corroborar empíricamente el comportamiento previsto de la viga bajo condiciones controladas, mitigando riesgos potenciales antes de la fabricación en serie o la instalación definitiva.
Factores Determinantes para la Propuesta de Prototipado y Ensayos
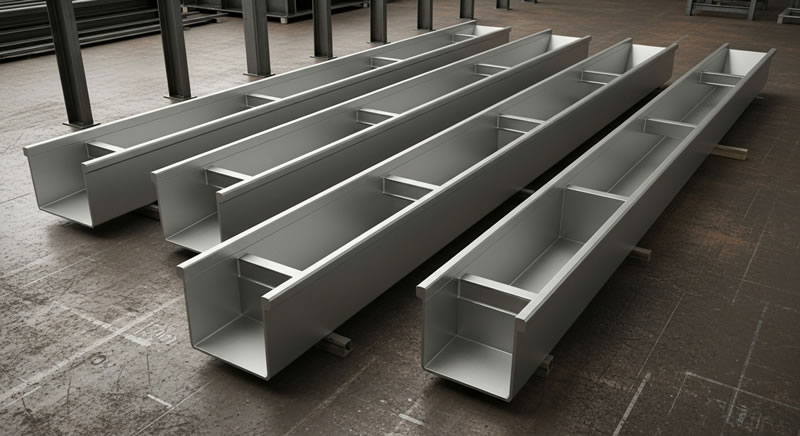
La decisión de embarcarse en la construcción y ensayo de un prototipo para una viga metálica personalizada no es arbitraria. Se fundamenta en una serie de factores técnicos y de gestión del riesgo cuidadosamente evaluados. Identificar estos factores es clave para justificar la inversión de tiempo y recursos que esta fase implica. Los principales catalizadores que nos llevan a proponer activamente el desarrollo de prototipos y ensayos específicos incluyen:
- Complejidad Inherente al Diseño:
- Geometría No Convencional: Vigas con curvaturas complejas, secciones variables de forma abrupta, grandes perforaciones o múltiples intersecciones pueden presentar comportamientos tensionales y de deformación difíciles de predecir con total certeza únicamente mediante modelos numéricos. La distribución de esfuerzos en zonas singulares puede ser particularmente sensible a pequeños detalles constructivos.
- Conexiones Innovadoras o Críticas: Cuando se diseñan uniones empernadas o soldadas que se apartan de las configuraciones estándar recogidas en la normativa (como la NSR-10 en Colombia) o que deben transmitir cargas muy elevadas o de naturaleza cíclica, un prototipo permite validar su resistencia, rigidez y ductilidad real.
- Uso de Materiales Avanzados o Combinaciones Inusuales: La introducción de aceros de ultra-alta resistencia, aceros inoxidables con comportamientos particulares o la combinación de acero con otros materiales estructurales en la misma viga puede requerir validación experimental si no existe suficiente data empírica sobre su interacción específica en la configuración diseñada.
- Mecanismos de Falla Complejos: Situaciones donde pueden interactuar diversos modos de falla (pandeo local, pandeo distorsional, pandeo global, plastificación, fractura) de manera compleja, haciendo que la predicción analítica del modo dominante y la capacidad última sea más incierta.
- Criticidad Estructural y Consecuencias de Falla:
- Componentes Clave en Infraestructuras Críticas: Vigas que forman parte esencial de puentes, viaductos, estadios, hospitales, centrales energéticas o edificios de gran altura en ciudades como Bogotá, donde una falla tendría consecuencias catastróficas en términos de vidas humanas, impacto económico y social.
- Elementos Sometidos a Cargas Extremas o Dinámicas: Vigas diseñadas para resistir sismos de gran magnitud (siguiendo los requisitos sismorresistentes de Colombia), vientos huracanados, explosiones, impactos o cargas de fatiga significativas (como en puentes grúa o estructuras soporte de maquinaria pesada). La validación experimental del comportamiento bajo estas condiciones extremas es invaluable.
- Aplicaciones con Bajos Márgenes de Seguridad o Requerimientos de Desempeño Muy Estrictos: Proyectos donde se busca optimizar al máximo el peso de la estructura o donde las tolerancias de deformación son mínimas, exigiendo una confianza muy alta en las predicciones de rigidez y resistencia.
- Falta de Precedentes o Normativa Específica Insuficiente:
- Diseños Verdaderamente Innovadores: Cuando la viga personalizada representa una solución estructural sin precedentes directos en la práctica constructiva o en la literatura técnica documentada. La ausencia de casos de estudio comparables incrementa la incertidumbre.
- Geometrías o Configuraciones No Cubiertas por Códigos: Situaciones donde las dimensiones, proporciones o detalles específicos de la viga o sus conexiones caen fuera del alcance explícito de las normativas de diseño vigentes, requiriendo una justificación más allá del cálculo normativo estándar.
- Necesidad de Validar Nuevos Procesos de Fabricación: Si la fabricación de la viga personalizada implica técnicas de soldadura, conformado o ensamblaje novedosas, un prototipo puede servir también para validar la viabilidad y la calidad del proceso productivo y su impacto en las propiedades finales del elemento.
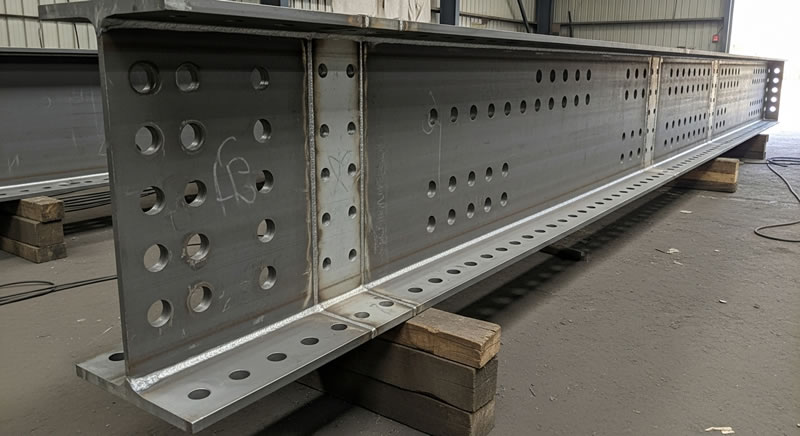
A continuación, se presenta una orientación sobre cuándo considerar prioritaria la fase de prototipado:
Factor Evaluado | Condición de Baja Prioridad para Prototipado | Condición de Media Prioridad para Prototipado | Condición de Alta Prioridad para Prototipado |
---|---|---|---|
Complejidad Geométrica | Geometría simple, prismática, secciones estándar. | Secciones variables moderadas, perforaciones estándar. | Curvaturas complejas, cambios abruptos de sección, grandes aberturas, múltiples intersecciones. |
Complejidad de Conexiones | Conexiones estándar según normativa, bien documentadas. | Conexiones ligeramente modificadas, cargas moderadas. | Conexiones innovadoras, no estándar, cargas muy altas, cargas cíclicas o de impacto. |
Criticidad Estructural | Componente secundario, falla con consecuencias localizadas y no catastróficas. | Componente primario en estructura convencional, consecuencias significativas pero manejables. | Componente clave en infraestructura crítica, falla con consecuencias catastróficas (vidas, economía). |
Naturaleza de las Cargas | Cargas estáticas, bien definidas, dentro de rangos habituales. | Cargas dinámicas moderadas, fatiga de bajo ciclo. | Cargas extremas (sismo severo, explosión), fatiga de alto ciclo, impacto. |
Novedad del Diseño | Diseño basado en prácticas establecidas y precedentes directos. | Diseño con algunas variaciones sobre soluciones conocidas. | Diseño completamente innovador, sin precedentes comparables. |
Cobertura Normativa | Diseño y detalles completamente cubiertos por la normativa vigente (ej. NSR-10). | Algunos aspectos en los límites o fuera del alcance explícito de la norma. | Configuración significativamente fuera del alcance normativo. |
La decisión final de proceder con prototipos y ensayos surge de una ponderación conjunta de estos factores. Un solo factor de alta prioridad puede ser suficiente para justificar esta fase, especialmente si se relaciona con la seguridad o la criticidad de la estructura. En proyectos desarrollados en Colombia, la consideración de las exigencias sísmicas locales a menudo añade un argumento de peso para la validación experimental de componentes críticos.
Diseño del Prototipo: Representatividad y Enfoque en la Validación
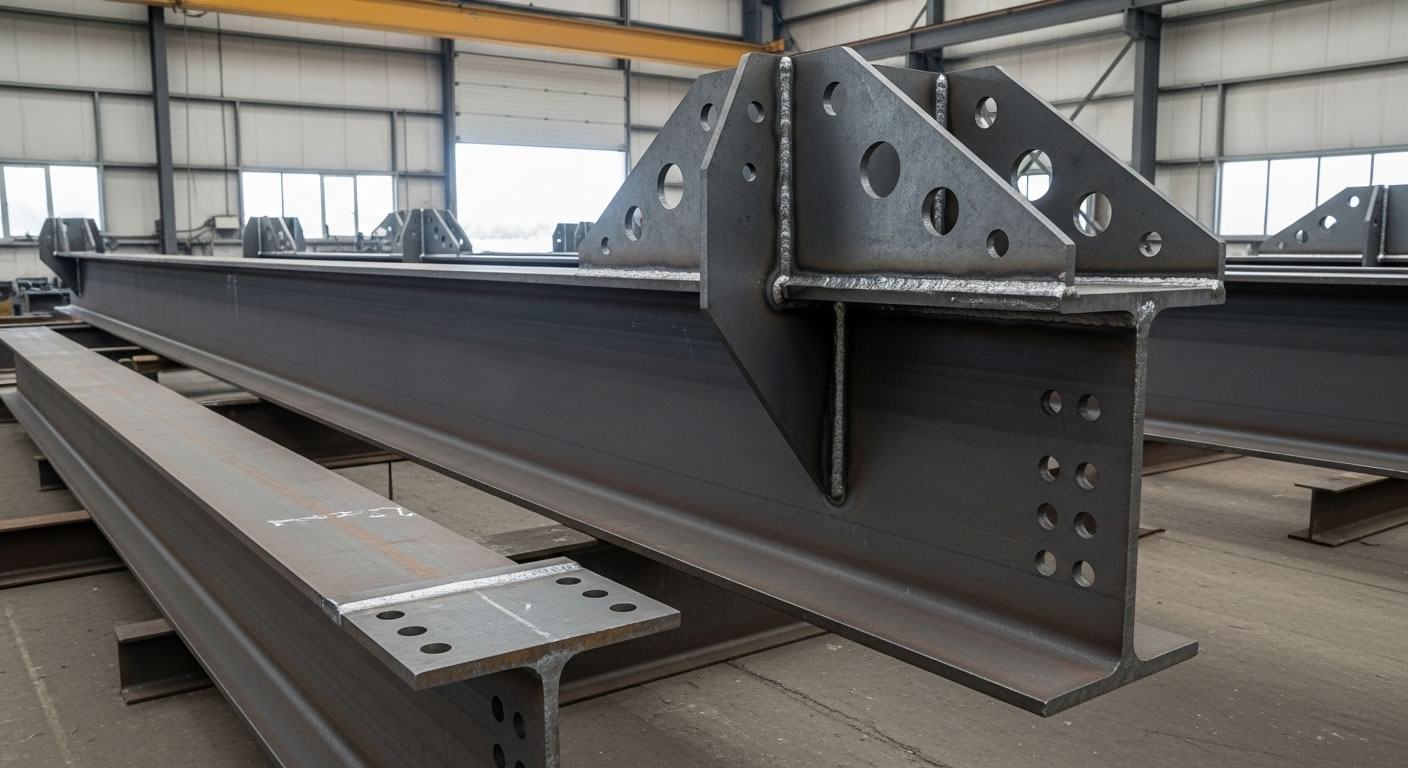
Una vez tomada la decisión de realizar un prototipo, su diseño es un paso crucial. El objetivo no es necesariamente replicar la viga completa en todos sus detalles si no es pertinente para la validación requerida. El diseño del prototipo debe ser una representación fiel y eficiente del aspecto específico que genera incertidumbre y que se busca validar experimentalmente. Los principios clave en el diseño del prototipo son:
- Escala del Prototipo:
- Escala Real (1:1): Es la opción preferida siempre que sea factible en términos de coste, manejo y capacidad de las instalaciones de ensayo. Elimina las incertidumbres asociadas a las leyes de escala y permite probar los materiales y procesos de fabricación reales. Es casi indispensable para validar detalles de conexión complejos o fenómenos dependientes del tamaño real, como el pandeo local en perfiles de pared delgada.
- Escala Reducida: Se utiliza cuando el prototipo a escala real es inviable por tamaño o coste. Requiere una aplicación cuidadosa de las teorías de similitud y las leyes de escala para asegurar que los resultados puedan ser extrapolados de manera fiable al comportamiento del elemento real. Es fundamental asegurar que los fenómenos físicos dominantes (ej. plastificación, pandeo) se repliquen correctamente a escala reducida. La elección de la escala (ej. 1:2, 1:5, 1:10) dependerá del fenómeno a estudiar y de las limitaciones prácticas. Pueden surgir dificultades en replicar exactamente detalles constructivos muy pequeños o propiedades de materiales dependientes de la microestructura.
- Nivel de Detalle y Alcance:
- Prototipo Completo vs. Sub-ensamblaje: No siempre es necesario ensayar la viga entera. Si la incertidumbre se concentra en una conexión específica, un detalle geométrico particular o el comportamiento de una sección transversal bajo flexión o cortante, se puede diseñar un prototipo que represente únicamente esa zona crítica (un sub-ensamblaje). Esto reduce costes y simplifica el montaje del ensayo. Por ejemplo, para validar una conexión viga-columna innovadora, se puede ensayar un montaje en "cruz" o en "T" que incluya la columna y los extremos de las vigas relevantes.
- Simplificaciones Justificadas: Se pueden omitir detalles del prototipo que no influyan significativamente en el fenómeno bajo estudio. Por ejemplo, si se valida la capacidad a flexión de una sección, quizás no sea necesario replicar con exactitud los rigidizadores de apoyo si estos no son el foco del análisis. Sin embargo, cualquier simplificación debe ser cuidadosamente justificada para no invalidar los resultados.
- Representación de las Condiciones de Contorno: El diseño del prototipo debe incluir los elementos necesarios para poder replicar en el laboratorio las condiciones de apoyo y carga que experimentará la viga real en la estructura. Esto es fundamental para que las mediciones de deformación y la distribución interna de esfuerzos sean representativas.
- Foco en el Aspecto a Validar:
- Identificación Clara del Objetivo: ¿Se quiere validar la capacidad última a flexión? ¿La rigidez rotacional de una conexión? ¿La resistencia a fatiga de una soldadura? ¿El comportamiento ante pandeo lateral-torsional? El diseño del prototipo y el plan de instrumentación deben estar directamente enfocados en medir las variables relevantes para responder a esta pregunta específica.
- Instrumentación Estratégica: El diseño del prototipo debe prever la ubicación óptima de los sensores (galgas extensométricas, LVDTs, etc.) para capturar la información necesaria. Se deben identificar las zonas de máximos esfuerzos, máximas deformaciones o puntos clave para entender el comportamiento global y local.
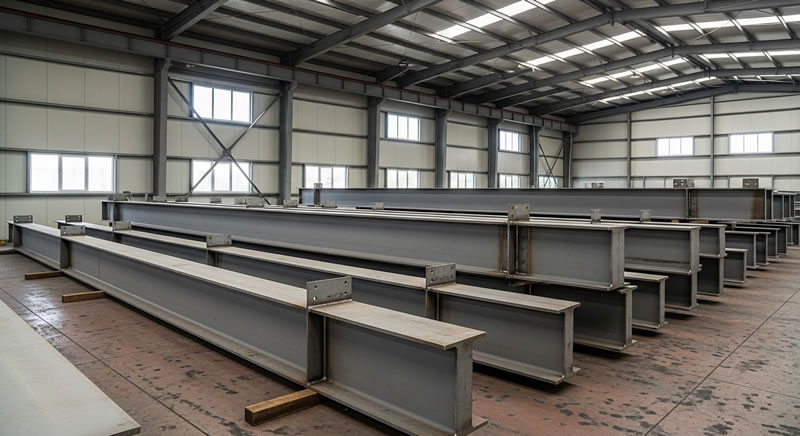
El proceso de diseño del prototipo es iterativo y colaborativo, involucrando a los ingenieros de diseño, los especialistas en ensayos y, a menudo, al equipo de fabricación. Se busca un equilibrio entre representatividad, coste, viabilidad del ensayo y claridad en la obtención de resultados interpretables. Un prototipo bien diseñado es aquel que permite obtener respuestas concluyentes a las preguntas específicas que motivaron su construcción.
A continuación, se comparan las características principales de prototipos a escala real frente a escala reducida:
Característica | Prototipo a Escala Real (1:1) | Prototipo a Escala Reducida |
---|---|---|
Representatividad de Materiales | Directa (se usan los mismos materiales). | Requiere cuidado si las propiedades del material dependen del tamaño o proceso de fabricación. Puede necesitar materiales modelo. |
Representatividad de Detalles Constructivos | Directa (soldaduras, pernos, tolerancias reales). | Difícil o imposible replicar detalles muy pequeños. Las tolerancias relativas pueden variar. |
Efectos de Escala | Inexistentes. Resultados directamente aplicables. | Presentes. Requiere aplicación de leyes de similitud para extrapolar resultados. Incertidumbre asociada. |
Coste de Fabricación | Generalmente alto (material, mano de obra). | Generalmente más bajo, pero requiere diseño y fabricación de precisión. |
Coste y Complejidad del Ensayo | Alto (grandes cargas, equipos robustos, manejo complejo). | Más bajo (menores cargas, equipos más pequeños, manejo más sencillo). |
Disponibilidad de Instalaciones de Ensayo | Limitada para elementos muy grandes o cargas muy altas. | Más amplia disponibilidad de laboratorios capaces. |
Aplicabilidad Principal | Validación de conexiones complejas, pandeo local, comportamiento de materiales específicos, procesos de fabricación. | Estudio del comportamiento global (flexión, cortante, torsión), pandeo global, fenómenos donde las leyes de escala son bien conocidas. |
Instrumentación para la Monitorización de Ensayos de Carga: Capturando el Comportamiento Real
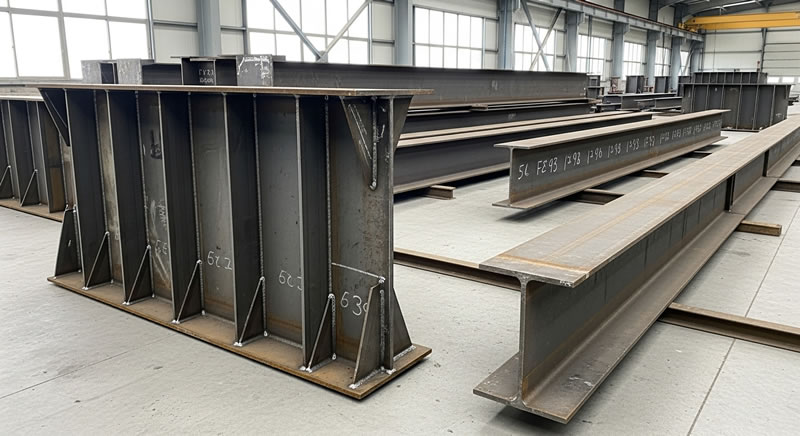
La esencia de un ensayo estructural reside en medir con precisión cómo responde el prototipo a las cargas aplicadas. La instrumentación es el conjunto de sensores y sistemas de adquisición de datos que permiten "ver" y cuantificar esta respuesta. La selección y colocación adecuada de los instrumentos son vitales para obtener datos útiles y fiables que permitan validar o refutar las hipótesis de diseño. Los tipos de instrumentación comúnmente utilizados en ensayos de carga de vigas metálicas personalizadas incluyen:
- Galgas Extensométricas (Strain Gauges):
- Principio: Pequeños sensores resistivos que se adhieren firmemente a la superficie del acero. Su resistencia eléctrica cambia proporcionalmente a la deformación unitaria (estiramiento o acortamiento) del material en el punto donde están adheridas.
- Propósito: Medir deformaciones locales con alta precisión. A partir de estas mediciones y conociendo el módulo de elasticidad del acero, se pueden calcular los esfuerzos (tensiones) en puntos específicos de la viga (alas, alma, zonas de conexión).
- Aplicaciones Típicas: Identificar zonas de concentración de esfuerzos, verificar la distribución de tensiones a lo largo de la sección transversal, detectar el inicio de la plastificación (fluencia) del acero, monitorizar deformaciones en soldaduras o alrededor de perforaciones.
- Tipos y Configuraciones: Existen galgas uniaxiales (miden deformación en una dirección), biaxiales y triaxiales (rosetas, miden el estado de deformación completo en un punto). Su selección depende del estado tensional esperado.
- Consideraciones: Requieren una preparación cuidadosa de la superficie y una correcta instalación y protección. La interpretación de los datos requiere conocimiento de la teoría de la elasticidad y plasticidad.
- Transductores de Desplazamiento Variable Lineal (LVDTs - Linear Variable Differential Transformers):
- Principio: Sensores electromecánicos que miden el desplazamiento lineal de un núcleo móvil dentro de un campo magnético generado por bobinas. Proporcionan una señal eléctrica proporcional al desplazamiento.
- Propósito: Medir desplazamientos absolutos o relativos entre puntos del prototipo o entre el prototipo y un punto de referencia fijo.
- Aplicaciones Típicas: Medir la flecha (deflexión vertical) en el centro del vano o en otros puntos de interés, medir desplazamientos horizontales (derivas), medir el deslizamiento relativo en conexiones empernadas, medir la apertura o cierre de fisuras, medir giros o rotaciones en los apoyos o en las conexiones (usando configuraciones específicas de LVDTs).
- Tipos y Rangos: Disponibles en una amplia variedad de rangos de medida (desde micrómetros hasta metros) y precisiones.
- Consideraciones: Requieren un montaje estable y puntos de referencia fijos y fiables. Su precisión puede verse afectada por vibraciones si no están bien instalados.
- Celdas de Carga (Load Cells):
- Principio: Transductores que convierten una fuerza aplicada (tracción o compresión) en una señal eléctrica medible. Generalmente se basan en la deformación de un elemento interno instrumentado con galgas extensométricas.
- Propósito: Medir con precisión la magnitud de las cargas aplicadas al prototipo por los actuadores hidráulicos o sistemas de carga, o medir las reacciones en los apoyos.
- Aplicaciones Típicas: Controlar y registrar la carga aplicada durante el ensayo, verificar que se alcanzan los niveles de carga deseados según el protocolo, medir las fuerzas internas transferidas a través de componentes específicos si se integran celdas de carga dentro del montaje.
- Tipos y Capacidades: Existen diversos tipos (de compresión, de tracción, tipo "S", tipo "pancake") y un amplio rango de capacidades, desde unos pocos Newtons hasta miles de KiloNewtons.
- Consideraciones: Deben ser calibradas periódicamente. Su correcta alineación con la dirección de la fuerza es importante para evitar errores de medición.
- Otros Instrumentos (Menos Comunes o para Aplicaciones Específicas):
- Inclinómetros o Clinómetros: Miden ángulos de inclinación o rotación directamente. Útiles para evaluar la rotación en apoyos o conexiones.
- Potenciómetros de Hilo (String Potentiometers): Miden desplazamientos lineales largos mediante un cable retráctil conectado a un potenciómetro rotativo. Alternativa a LVDTs para grandes desplazamientos.
- Sistemas de Medición Óptica (Fotogrametría, Correlación Digital de Imágenes - DIC): Técnicas sin contacto que permiten medir campos de deformación y desplazamiento en superficies completas del prototipo analizando imágenes tomadas durante el ensayo. Muy potentes para visualizar patrones de deformación complejos y detectar localizaciones de daño.
- Sensores Acústicos (Emisión Acústica): Detectan ondas de ultrasonido generadas por el crecimiento de microfisuras o la plastificación localizada dentro del material, permitiendo monitorizar la iniciación y propagación del daño.
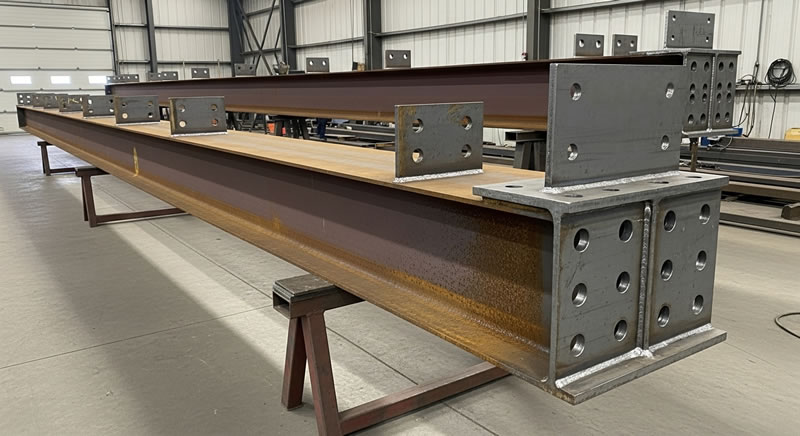
La selección final de la instrumentación depende de los objetivos del ensayo, el tipo de viga, las magnitudes esperadas de carga y deformación, el presupuesto y la precisión requerida. Un plan de instrumentación bien concebido es esencial para extraer el máximo valor del ensayo del prototipo.
A continuación, se resumen los instrumentos principales y su función primordial en ensayos de vigas:
Tipo de Instrumento | Magnitud Medida Principalmente | Propósito Clave en Ensayo de Vigas | Información Derivada |
---|---|---|---|
Galgas Extensométricas | Deformación Unitaria Local (µ?) | Evaluar niveles de esfuerzo en puntos críticos. Detectar inicio de fluencia. Validar distribución de tensiones. | Esfuerzo (Tensión), Curvatura Local. |
Transductores de Desplazamiento (LVDTs) | Desplazamiento Lineal (mm) | Medir flechas (deflexiones). Medir desplazamientos en apoyos o conexiones. Medir acortamientos o alargamientos globales. | Rigidez Global, Ductilidad, Modos de Deformación. |
Celdas de Carga | Fuerza (kN) | Medir y controlar la carga aplicada. Medir reacciones en los apoyos. | Curva Carga-Desplazamiento, Capacidad Última, Resistencia de Conexiones. |
Inclinómetros / Clinómetros | Ángulo de Rotación (grados, radianes) | Medir giros en apoyos o conexiones. Evaluar rigidez rotacional. | Rigidez a Flexión, Rigidez de Conexión. |
Sistemas Ópticos (DIC) | Campo de Deformación / Desplazamiento Superficial | Visualizar patrones de deformación complejos. Detectar localización de daño. Medir deformaciones sin contacto. | Mapas de Esfuerzo/Deformación, Identificación de Modos de Pandeo. |
Definición del Protocolo de Ensayo: Simulando la Realidad y Explorando los Límites
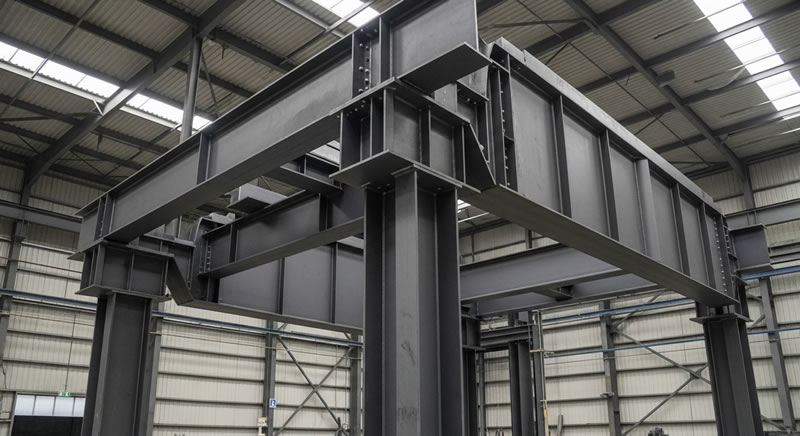
Un ensayo estructural no es simplemente aplicar carga hasta que algo falle. Requiere un plan detallado, un protocolo de ensayo, que defina cómo se aplicarán las cargas, qué se medirá y en qué secuencia se realizarán las operaciones. El objetivo del protocolo es doble: simular las condiciones de servicio que la viga experimentará durante su vida útil y, a menudo, explorar su comportamiento más allá de esas condiciones, hasta alcanzar estados límite o la falla, para comprender sus márgenes de seguridad y modos de fallo.
La definición del protocolo de ensayo es una tarea crítica que debe considerar:
- Simulación de las Condiciones de Servicio Reales:
- Tipos de Carga: Identificar las cargas relevantes que actuaron sobre la viga en la estructura real: carga muerta (peso propio, acabados), carga viva (ocupación, mobiliario, nieve), carga de viento, carga sísmica, cargas térmicas, cargas de maquinaria, etc. El protocolo debe intentar replicar los efectos combinados más desfavorables de estas cargas.
- Naturaleza de la Carga: ¿Son las cargas predominantemente estáticas (aplicadas lentamente y mantenidas) o dinámicas (variables en el tiempo, como sismos o vibraciones)? El protocolo debe reflejar esto. Los ensayos estáticos son más comunes para validar resistencia y rigidez, mientras que los ensayos dinámicos (ej. en mesa vibratoria, con actuadores rápidos) son necesarios para evaluar la respuesta sísmica o a fatiga.
- Distribución de la Carga: ¿La carga real es uniformemente distribuida, concentrada en puntos específicos, o sigue un patrón más complejo? El sistema de aplicación de carga en el laboratorio (ej. mediante uno o varios actuadores hidráulicos, vigas repartidoras) debe diseñarse para reproducir lo más fielmente posible esta distribución sobre el prototipo.
- Condiciones de Apoyo: Replicar las condiciones de contorno reales (apoyos simples, empotramientos, apoyos elásticos) es fundamental, ya que determinan cómo se distribuyen los esfuerzos internos en la viga. El diseño de los apoyos en el montaje de ensayo es tan importante como la aplicación de la carga.
- Exploración de Condiciones Extremas y Estados Límite:
- Niveles de Carga Incrementales: Los ensayos suelen realizarse aplicando la carga en pasos o incrementos controlados. Esto permite observar la evolución del comportamiento de la viga (lineal elástico, inicio de fluencia, comportamiento no lineal, redistribución de esfuerzos) a medida que aumenta la carga.
- Carga hasta la Falla (Ensayo Destructivo): A menudo, el objetivo es llevar el prototipo hasta su capacidad última o hasta un nivel de deformación considerado como falla funcional. Esto proporciona información invaluable sobre el modo de falla real (pandeo, plastificación excesiva, fractura), la ductilidad del elemento y el margen de seguridad real respecto a las cargas de diseño.
- Ciclos de Carga y Descarga: Aplicar ciclos de carga y descarga a diferentes niveles puede ayudar a evaluar la rigidez efectiva, el daño acumulado, la recuperación elástica y el comportamiento histerético (disipación de energía), especialmente relevante para cargas sísmicas o de fatiga.
- Simulación de Escenarios Extremos Específicos: Para proyectos en zonas sísmicas como Bogotá y gran parte de Colombia, el protocolo puede incluir la aplicación de historias de desplazamiento o aceleración representativas de sismos de diseño o sismos máximos considerados, utilizando actuadores dinámicos o mesas vibratorias si es necesario.
- Definición de la Secuencia y Duración del Ensayo:
- Velocidad de Aplicación de Carga: En ensayos estáticos, la carga se aplica lentamente para evitar efectos dinámicos y permitir que el material se estabilice en cada paso. La velocidad debe ser controlada y registrada.
- Mantenimiento de Carga: En algunos casos, puede ser necesario mantener un nivel de carga constante durante un período para evaluar efectos dependientes del tiempo como el 'creep' (fluencia lenta), aunque esto es más relevante para otros materiales como el hormigón.
- Número de Ciclos (Ensayos de Fatiga): Para evaluar la resistencia a fatiga, el protocolo define el número de ciclos de carga a aplicar, la amplitud de la carga (rango de esfuerzo) y la frecuencia. Pueden ser millones de ciclos para fatiga de alto ciclo (ej. puentes) o cientos/miles para fatiga de bajo ciclo (ej. sismo).
- Criterios de Parada o Finalización: El protocolo debe establecer claramente cuándo se considera que el ensayo ha finalizado: alcanzar un nivel de carga predefinido, alcanzar una deformación límite, observar un modo de falla específico, o la rotura del prototipo.
- Registro de Datos y Observaciones:
- Frecuencia de Adquisición: Definir la frecuencia con la que se registrarán los datos de todos los sensores. Mayor frecuencia para ensayos dinámicos o para capturar eventos rápidos como la falla.
- Observaciones Visuales y Documentación: El protocolo debe incluir puntos de inspección visual, toma de fotografías y vídeos en etapas clave del ensayo para documentar el comportamiento, la aparición de fisuras, deformaciones visibles, modos de pandeo, etc.
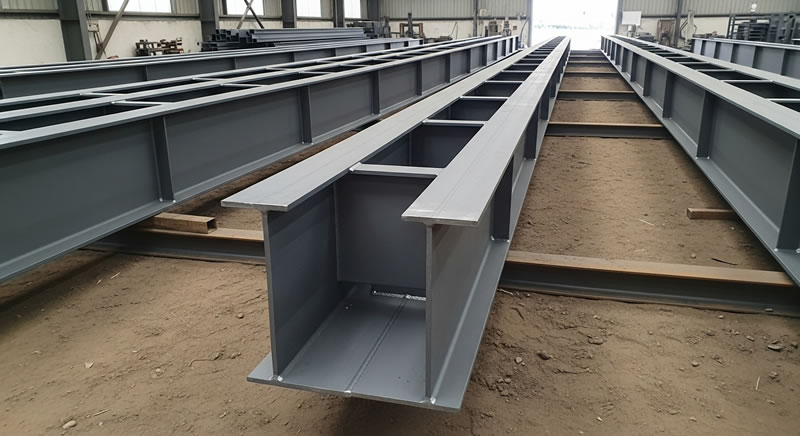
Un protocolo de ensayo bien definido asegura que el experimento sea repetible, que los datos obtenidos sean relevantes para los objetivos planteados y que se maximice la información obtenida de la inversión realizada en el prototipo. Este protocolo se documenta formalmente y se sigue rigurosamente durante la ejecución del ensayo.
A continuación, se presentan ejemplos de enfoques de protocolos según el objetivo del ensayo:
Objetivo del Ensayo | Tipo de Carga Principal | Niveles de Carga Clave | Aspecto Central del Protocolo | Duración / Ciclos |
---|---|---|---|---|
Validar Resistencia y Rigidez Estática | Estática, Monotónica Creciente | Cargas de servicio, Carga de diseño (mayorada), Carga última (hasta falla). | Incrementos de carga controlados, medición precisa de carga vs deformación. | Horas (ensayo lento). Un ciclo principal. |
Evaluar Comportamiento Sísmico | Dinámica Cíclica (Desplazamiento o Fuerza) | Ciclos a niveles crecientes de deriva o fuerza, basados en espectro de diseño sísmico (ej. NSR-10). | Aplicación de historia de ciclos predefinida, medición de histéresis (energía disipada), observación de modos de falla dúctiles/frágiles. | Horas. Decenas o cientos de ciclos. |
Evaluar Resistencia a Fatiga | Dinámica Cíclica (Fuerza Constante o Variable) | Ciclos alrededor de una carga media, con una amplitud de esfuerzo definida. | Aplicación de un gran número de ciclos a frecuencia constante, detección de inicio y propagación de fisuras. | Días o semanas. Millones de ciclos (alto ciclo) o miles (bajo ciclo). |
Validar Comportamiento de Conexión | Estática o Cíclica (según aplicación) | Niveles que induzcan fluencia en componentes, deslizamiento en pernos, hasta capacidad última de la conexión. | Medición detallada de deformaciones y rotaciones locales en la conexión, observación del modo de falla (pernos, soldadura, placa). | Variable según el tipo de carga. |
Verificar Modo de Pandeo | Estática, Monotónica Creciente | Carga crítica de pandeo teórica, carga post-pandeo. | Observación cuidadosa de la aparición de deformaciones por pandeo (local, distorsional, global), medición de cargas y deformaciones asociadas. | Horas. Un ciclo principal. |
Instalaciones de Ensayo Disponibles o Accesibles: La Infraestructura para la Validación
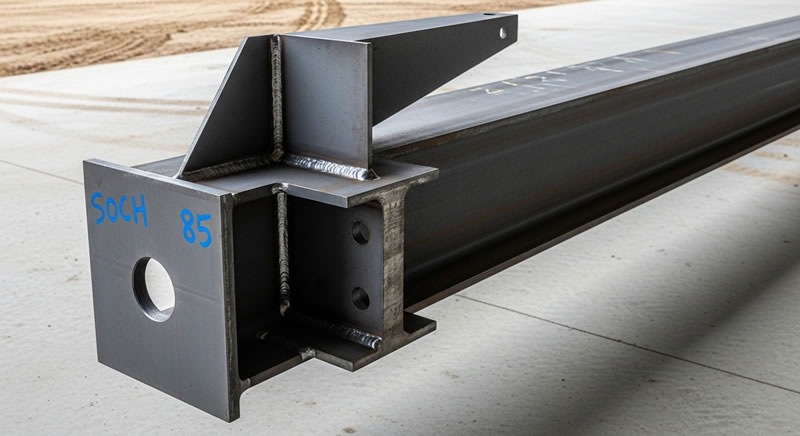
La realización de ensayos estructurales sobre prototipos de vigas metálicas, especialmente si son de tamaño considerable o requieren cargas elevadas, demanda instalaciones especializadas. La disponibilidad o el acceso a esta infraestructura es un factor logístico clave en la viabilidad de la fase de prototipado. En Colombia, y particularmente en centros de desarrollo e investigación como los que pueden encontrarse en Bogotá o en universidades con facultades de ingeniería civil robustas, existen capacidades para llevar a cabo una variedad de ensayos estructurales. Las instalaciones típicas necesarias o deseables incluyen:
- Pórticos o Marcos de Carga:
- Descripción: Estructuras de acero o concreto muy robustas y rígidas, diseñadas para reaccionar contra las altas fuerzas aplicadas a los especímenes de ensayo. Pueden tener configuraciones diversas (un solo pórtico, marcos tridimensionales).
- Función: Proveen los puntos de anclaje fijos necesarios para los actuadores que aplican la carga y para los apoyos del prototipo. Deben ser significativamente más resistentes y rígidos que el prototipo para no influir en la medición de su comportamiento.
- Capacidad: Varían enormemente en tamaño y capacidad de carga, desde pequeños marcos para ensayar componentes hasta grandes estructuras capaces de soportar cientos o miles de toneladas de fuerza.
- Suelos Resistentes (Strong Floors):
- Descripción: Losas de cimentación de concreto armado de gran espesor y resistencia, con una retícula de puntos de anclaje embebidos (insertos roscados) a intervalos regulares.
- Función: Permiten montar configuraciones de ensayo muy flexibles y de gran tamaño directamente sobre el suelo, anclando tanto el prototipo como los sistemas de carga y reacción en cualquier posición deseada. Son ideales para ensayar estructuras completas o sub-ensamblajes grandes.
- Flexibilidad: La retícula de anclajes ofrece una gran versatilidad para adaptar el montaje a geometrías complejas o para aplicar cargas en múltiples direcciones.
- Muros de Reacción (Reaction Walls):
- Descripción: Estructuras verticales de concreto armado o acero, a menudo en forma de "L" o "U" combinadas con un suelo resistente. También cuentan con puntos de anclaje.
- Función: Permiten aplicar cargas horizontales significativas a los prototipos, simulando acciones como el sismo o el viento. Son esenciales para ensayos pseudo-dinámicos o cíclicos de componentes estructurales sometidos a fuerzas laterales.
- Importancia en Colombia: Dada la sismicidad del país, la disponibilidad de muros de reacción robustos es crucial para validar experimentalmente el comportamiento de vigas y conexiones diseñadas bajo criterios sismorresistentes como los de la NSR-10.
- Actuadores Hidráulicos o Eléctricos:
- Descripción: Dispositivos que generan y aplican las fuerzas o desplazamientos controlados sobre el prototipo. Los actuadores hidráulicos son los más comunes para altas cargas, ofreciendo gran fuerza y capacidad de control. Los actuadores eléctricos (servomotores) se usan para cargas menores o aplicaciones que requieren alta precisión o velocidad.
- Función: Son el "músculo" del sistema de ensayo. Pueden operar en control de fuerza (aplicando una carga específica) o en control de desplazamiento (imponiendo una deformación específica).
- Capacidades: Varían en capacidad de fuerza (desde pocos kN hasta varios MN), carrera (rango de movimiento, desde mm hasta metros) y velocidad (para ensayos estáticos lentos o dinámicos rápidos).
- Sistemas de Control y Adquisición de Datos (DAQ):
- Descripción: El "cerebro" y los "sentidos" del sistema de ensayo. Incluye el hardware (unidades de adquisición, acondicionadores de señal) y el software necesarios para controlar los actuadores según el protocolo definido y para registrar simultáneamente las lecturas de todos los sensores (galgas, LVDTs, celdas de carga, etc.).
- Función: Aseguran la correcta ejecución del ensayo, la sincronización de las mediciones y el almacenamiento seguro y organizado de los datos experimentales.
- Capacidades: Varían en número de canales (cuántos sensores pueden leer simultáneamente), velocidad de muestreo (cuántas lecturas por segundo), precisión y capacidades de procesamiento de datos en tiempo real.
- Equipamiento Auxiliar:
- Puentes Grúa y Equipos de Manejo: Necesarios para posicionar y manipular prototipos pesados dentro del laboratorio.
- Instrumentación de Medición y Calibración: Equipos para verificar las dimensiones del prototipo, calibrar los sensores y los actuadores.
- Sistemas de Iluminación y Cámaras: Para la documentación visual detallada del ensayo.
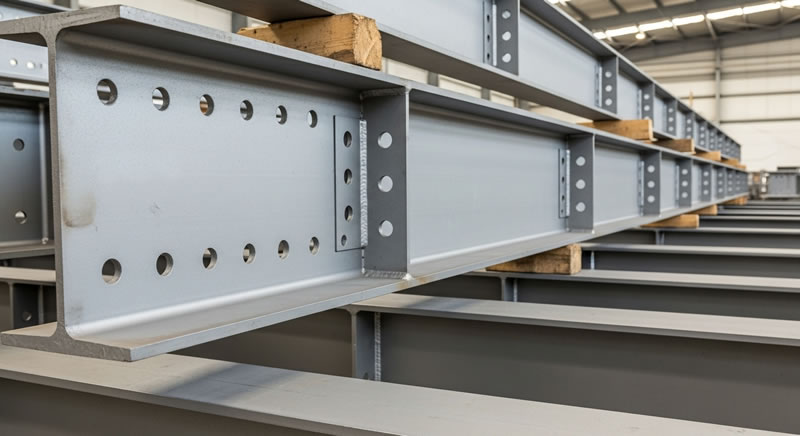
La elección de las instalaciones adecuadas dependerá del tamaño del prototipo, los niveles de carga requeridos, la complejidad del montaje y si se necesitan ensayos estáticos o dinámicos. Para proyectos de gran envergadura en Colombia, puede ser necesario recurrir a laboratorios universitarios especializados o centros de investigación que cuenten con la infraestructura de mayor capacidad, como los existentes en algunas de las principales universidades de Bogotá o Medellín.
A continuación, se indica la idoneidad de ciertas instalaciones para tipos específicos de ensayos:
Tipo de Ensayo Requerido | Instalación Clave Necesaria | Componente Adicional Importante |
---|---|---|
Ensayo de Viga a Flexión Estática (tamaño moderado) | Pórtico de Carga | Actuador Hidráulico de Capacidad Media, Celda de Carga, LVDTs, Galgas Extensométricas. |
Ensayo de Viga a Flexión Estática (tamaño grande / alta carga) | Suelo Resistente o Pórtico de Alta Capacidad | Actuadores Hidráulicos de Alta Capacidad, Sistema DAQ multicanal. |
Ensayo Cíclico de Conexión Viga-Columna (Simulación Sísmica Lenta) | Muro de Reacción y/o Suelo Resistente | Actuador Hidráulico con control de desplazamiento, LVDTs para medir rotación, Galgas en zona de conexión. |
Ensayo Dinámico de Viga (ej. en Mesa Vibratoria) | Mesa Vibratoria Sísmica | Acelerómetros, Sistema DAQ de alta velocidad. |
Ensayo de Pandeo Lateral-Torsional | Pórtico de Carga o Suelo Resistente | Sistema de aplicación de carga que permita el pandeo, LVDTs para medir desplazamientos laterales y torsión. |
Ensayo de Fatiga de Detalle Soldado | Marco de Carga específico para Fatiga | Actuador de Fatiga (alta frecuencia), Sistema de detección de fisuras (visual, NDT). |
Análisis y Correlación de Datos del Ensayo con Predicciones de Modelos
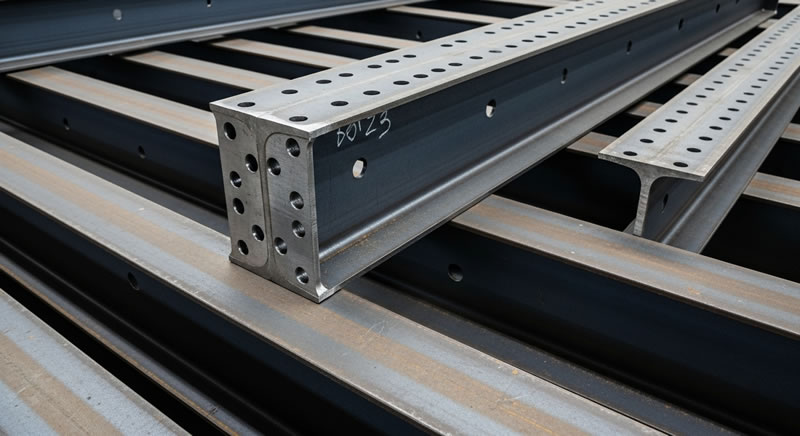
Una vez concluido el ensayo y recopilados los datos de la instrumentación, comienza una fase igualmente importante: el análisis y la interpretación de los resultados. El objetivo final no es solo observar qué sucedió, sino entender por qué sucedió y cómo se compara ese comportamiento real con las predicciones realizadas durante la fase de diseño, generalmente mediante cálculos manuales basados en normativas o, más comúnmente en casos complejos, mediante modelos de Elementos Finitos (FEA).
El proceso de análisis y correlación típicamente involucra los siguientes pasos:
- Procesamiento de Datos Crudos:
- Filtrado y Limpieza: Eliminar ruido o lecturas espurias de las señales de los sensores.
- Conversión a Unidades de Ingeniería: Convertir las señales eléctricas (voltajes, resistencias) a magnitudes físicas relevantes (fuerza en kN, desplazamiento en mm, deformación unitaria en µ?, esfuerzo en MPa).
- Cálculos Derivados: Calcular magnitudes adicionales a partir de las mediciones directas, como curvaturas a partir de galgas, rotaciones a partir de LVDTs, rigideces a partir de pendientes de curvas carga-desplazamiento.
- Representación Gráfica de Resultados:
- Curvas Carga-Desplazamiento: Representar la carga aplicada (eje Y) frente a una medida clave de desplazamiento o deformación (eje X), como la flecha en el centro del vano. Estas curvas son fundamentales para evaluar la rigidez, la resistencia y la ductilidad.
- Curvas Esfuerzo-Deformación: Graficar el esfuerzo calculado a partir de galgas frente a la deformación medida por las mismas, para evaluar el comportamiento del material en puntos específicos (lineal elástico, fluencia, endurecimiento por deformación).
- Mapas de Contorno (si se usó DIC): Visualizar la distribución de deformaciones o desplazamientos sobre la superficie del prototipo.
- Gráficos de Histéresis (para ensayos cíclicos): Representar la carga frente al desplazamiento a lo largo de los ciclos para visualizar la disipación de energía y la degradación de rigidez/resistencia.
- Comparación Cuantitativa con las Predicciones:
- Rigidez: Comparar la pendiente inicial (rigidez elástica) y la pendiente secante en diferentes niveles de carga de la curva experimental carga-desplazamiento con la rigidez predicha por el modelo FEA o los cálculos.
- Resistencia: Comparar la carga máxima alcanzada en el ensayo (capacidad última experimental) con la capacidad predicha por el modelo. Calcular el ratio Experimental/Predicho.
- Deformaciones y Esfuerzos Locales: Comparar las lecturas de galgas extensométricas y LVDTs en ubicaciones específicas con los valores predichos por el FEA en los mismos puntos.
- Modos de Falla: Comparar el modo de falla observado en el ensayo (ej. pandeo local del ala, plastificación de la sección, fractura de soldadura) con el modo de falla predicho por el análisis.
- Análisis de Discrepancias:
- Identificación de Diferencias Significativas: Determinar dónde y por qué el comportamiento real difiere del predicho. ¿El modelo sobreestimó o subestimó la rigidez/resistencia? ¿Predijo un modo de falla diferente?
- Investigación de Causas: Las discrepancias pueden deberse a múltiples factores:
- Propiedades reales del material diferentes de las asumidas en el modelo (límite elástico, módulo E).
- Dimensiones geométricas reales (espesores, tolerancias) diferentes de las nominales.
- Imperfecciones geométricas iniciales no consideradas adecuadamente en el modelo.
- Condiciones de contorno (apoyos, aplicación de carga) en el ensayo ligeramente diferentes de las idealizadas en el modelo.
- Efectos de esfuerzos residuales de la fabricación (soldadura, laminado) no incluidos en el modelo.
- Limitaciones inherentes al propio modelo FEA (tipo de elemento, malla, simplificaciones).
- Refinamiento del Modelo (si es necesario):
- Calibración: Utilizar los datos experimentales para ajustar parámetros inciertos en el modelo FEA (ej. propiedades del material, rigidez de conexiones semi-rígidas, nivel de imperfecciones) hasta que las predicciones del modelo se ajusten mejor a los resultados del ensayo.
- Validación Cruzada: Un modelo calibrado con un ensayo debería ser capaz de predecir razonablemente bien los resultados de otros ensayos similares o el comportamiento de la estructura real.
- Mejora de la Comprensión: El proceso de correlación y refinamiento profundiza la comprensión del ingeniero sobre el comportamiento real de la viga y sobre la precisión y limitaciones de las herramientas de análisis utilizadas.
La correlación entre ensayo y análisis es un diálogo bidireccional. El ensayo valida (o invalida) el modelo, y el modelo ayuda a interpretar los resultados del ensayo y a extrapolarlos a otras condiciones de carga o variantes de diseño. Una buena correlación aumenta significativamente la confianza en la capacidad del modelo para predecir el comportamiento de la viga final en la estructura real.
Realización de Ensayos Funcionales Adicionales
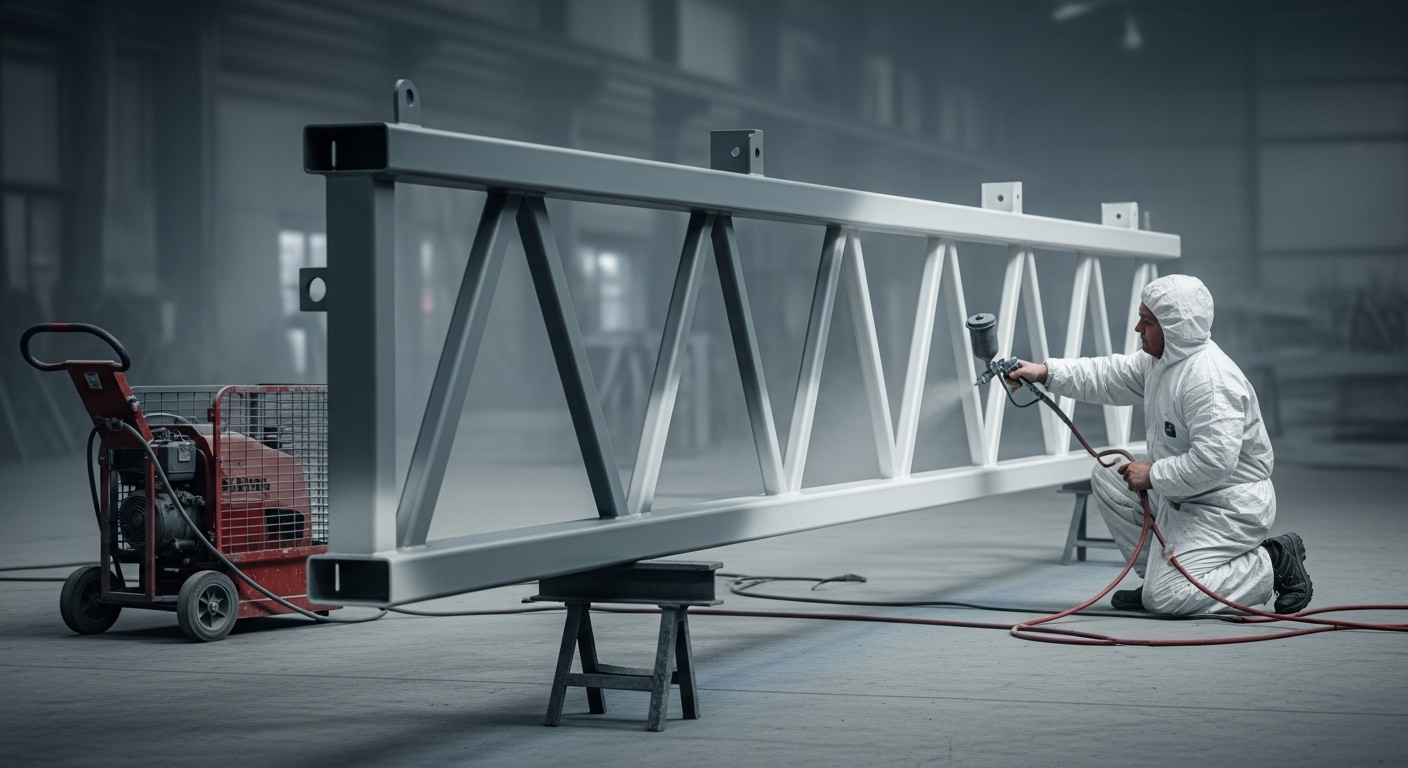
Si bien los ensayos de carga estructural son los más comunes para validar la resistencia y rigidez, en el contexto de vigas personalizadas para proyectos especiales, pueden surgir necesidades de realizar otros tipos de ensayos, denominados funcionales, sobre los prototipos. Estos ensayos se enfocan en aspectos operativos, de montaje o de interacción con otros sistemas, que también pueden ser críticos para el éxito del proyecto.
Algunos ejemplos de ensayos funcionales que podrían realizarse incluyen:
- Ensayos de Montaje o Ensamblaje:
- Propósito: Verificar la facilidad, precisión y viabilidad del proceso de montaje de la viga en obra, especialmente si involucra conexiones complejas, tolerancias ajustadas o secuencias de ensamblaje críticas.
- Ejecución: Se realiza un montaje de prueba del prototipo (o de las partes relevantes de la conexión) en condiciones controladas de taller o, si es posible, en un entorno que simule las restricciones del sitio. Se verifica el ajuste de las piezas, el acceso para herramientas (llaves de torque, equipos de soldadura), la alineación y el cumplimiento de las tolerancias especificadas.
- Beneficios: Permite identificar problemas potenciales de montaje antes de llegar a la obra, optimizar los procedimientos de ensamblaje, refinar detalles de diseño para facilitar la construcción y reducir tiempos y costes de instalación. Esto es particularmente valioso en ciudades con espacios de trabajo congestionados como Bogotá.
- Ensayos de Operación de Partes Móviles (si aplica):
- Propósito: Si la viga personalizada incorpora o soporta componentes móviles (ej. parte de un puente levadizo, soporte para una compuerta móvil, elemento de una cubierta retráctil), se puede necesitar verificar el correcto funcionamiento de estos mecanismos.
- Ejecución: Se opera el mecanismo repetidamente sobre el prototipo, monitorizando su suavidad de movimiento, la ausencia de atascos, el cumplimiento de los recorridos esperados y la interacción con la estructura de la viga bajo diferentes condiciones (con y sin carga estructural).
- Beneficios: Asegura que la viga, además de ser estructuralmente sólida, cumple con los requisitos funcionales de operación del sistema del que forma parte. Permite detectar problemas de interferencia, desgaste prematuro o mal funcionamiento.
- Ensayos de Interfaz con Otros Sistemas:
- Propósito: Verificar cómo la viga personalizada interactúa con otros elementos constructivos o sistemas (ej. fachadas, instalaciones MEP - Mecánicas, Eléctricas, Plomería) que se conectan a ella o pasan a través de ella.
- Ejecución: Se puede construir un 'mock-up' o maqueta a escala real que incluya el prototipo de la viga y los elementos adyacentes relevantes, para verificar físicamente los puntos de conexión, los espacios libres, las tolerancias de instalación y la compatibilidad entre sistemas.
- Beneficios: Previene conflictos y problemas de coordinación durante la fase de construcción, asegurando que todos los componentes encajen y funcionen juntos como se diseñó.
- Ensayos de Estanqueidad o Aislamiento (menos común para vigas):
- Propósito: En aplicaciones muy especiales donde la viga forma parte de un cerramiento o requiere propiedades específicas de aislamiento (térmico, acústico) o estanqueidad.
- Ejecución: Se somete el prototipo a pruebas específicas para medir la infiltración de aire o agua, la transmisión de calor o sonido, según los requisitos del proyecto.
- Beneficios: Valida el cumplimiento de requisitos funcionales no estructurales que pueden ser críticos para ciertas aplicaciones.
La necesidad de realizar ensayos funcionales dependerá enteramente de la naturaleza específica de la viga personalizada y del proyecto especial para el que se destina. Estos ensayos complementan la validación estructural, ofreciendo una visión más holística del desempeño del componente diseñado.
Documentación Visual del Proceso y Resultados del Ensayo
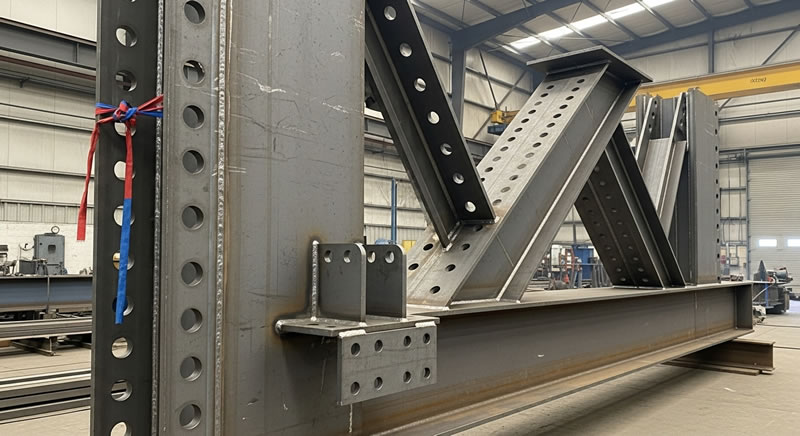
Un ensayo estructural, especialmente de un prototipo para un proyecto especial, es un evento rico en información visual. La documentación visual cuidadosa y sistemática es fundamental no solo para registrar lo que ocurrió, sino también para facilitar el análisis posterior, la comunicación de resultados y como evidencia del proceso de validación.
Las prácticas estándar para la documentación visual incluyen:
- Fotografía de Alta Resolución:
- Antes del Ensayo: Fotografías detalladas del prototipo montado, mostrando la configuración general, los detalles de las conexiones, la ubicación de la instrumentación (galgas, LVDTs), las condiciones de apoyo y el sistema de aplicación de carga.
- Durante el Ensayo: Fotografías en etapas clave definidas en el protocolo (ej. al alcanzar ciertos niveles de carga, al observar eventos significativos como fluencia visible, pandeo incipiente, formación de fisuras). Se debe documentar la lectura de carga y desplazamiento correspondiente si es posible.
- Después del Ensayo (Falla): Fotografías exhaustivas del prototipo fallado, mostrando claramente el modo de falla, la extensión del daño, las deformaciones permanentes, fracturas, etc. Primeros planos de las zonas críticas son esenciales.
- Escala y Referencia: Incluir reglas o elementos de escala conocida en las fotografías para poder estimar dimensiones.
- Videografía:
- Vídeo a Velocidad Normal: Grabar el desarrollo completo del ensayo o secciones significativas del mismo. Permite observar la secuencia de eventos, la evolución de las deformaciones y el comportamiento general del prototipo.
- Vídeo a Cámara Lenta (High-Speed): Extremadamente útil para capturar eventos rápidos y transitorios, como la propagación de una fractura, el pandeo súbito o el comportamiento durante un impacto o un ensayo dinámico rápido. Permite analizar en detalle mecanismos de falla que ocurren en fracciones de segundo.
- Múltiples Ángulos: Utilizar varias cámaras desde diferentes ángulos para obtener una visión completa del comportamiento tridimensional del prototipo.
- Registros y Anotaciones:
- Bitácora del Ensayo: Un registro escrito detallado que acompaña la ejecución, anotando la hora, el nivel de carga/desplazamiento, las observaciones visuales relevantes (ruidos, eventos inesperados, inicio de fenómenos), cualquier ajuste realizado al montaje o al protocolo.
- Marcado del Prototipo: Marcar directamente sobre el prototipo (con pintura o marcadores) la ubicación de plastificaciones (usando a veces líquidos penetrantes o recubrimientos especiales que se agrietan), la trayectoria de fisuras, las líneas de pandeo, etc., y fotografiar estas marcas.
- Integración con Datos Numéricos:
- Sincronización: Intentar sincronizar las grabaciones de vídeo y las fotografías con los datos numéricos registrados por el sistema DAQ, para poder correlacionar exactamente un evento visual con las lecturas de los sensores en ese instante.
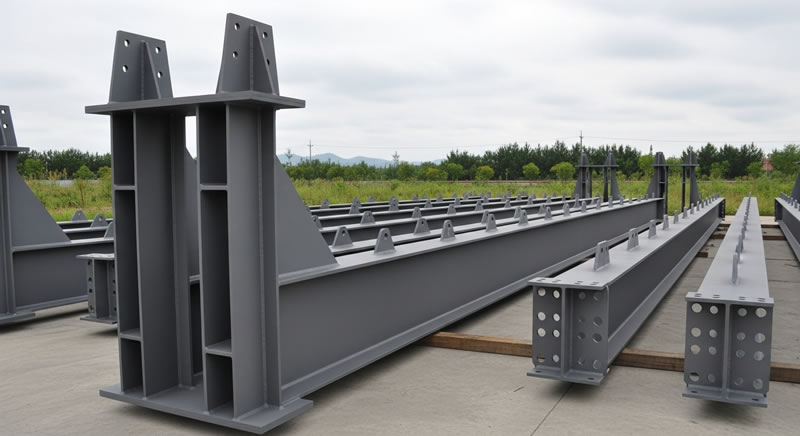
Esta documentación visual no es un mero añadido; es una parte integral del análisis. Permite:
- Confirmar y comprender los modos de falla identificados a partir de los datos numéricos.
- Detectar fenómenos inesperados o comportamientos locales no capturados por la instrumentación puntual.
- Facilitar la comunicación de los resultados a todas las partes interesadas (diseñadores, cliente, fabricantes, autoridades revisoras) de una manera clara e intuitiva.
- Servir como archivo histórico y base de conocimiento para futuros proyectos.
La calidad y exhaustividad de la documentación visual reflejan el rigor con el que se ha llevado a cabo la fase de ensayo y validación.
Implementación de Cambios en el Diseño Final Basados en Hallazgos
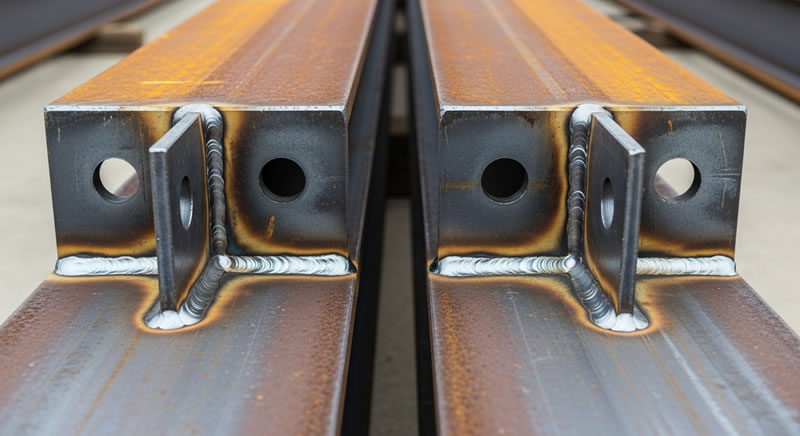
El propósito último de desarrollar un prototipo y realizar ensayos específicos no es solo obtener datos, sino utilizar esa información para mejorar y validar el diseño final de la viga personalizada. Los hallazgos del ensayo, ya sean confirmatorios o reveladores de discrepancias o debilidades, deben retroalimentar el proceso de diseño de manera estructurada.
El proceso para implementar cambios basados en los resultados experimentales generalmente sigue estos pasos:
- Análisis Crítico de Resultados: Comparar detalladamente los resultados experimentales (resistencia, rigidez, modos de falla, comportamiento local) con las predicciones del diseño original y los requisitos del proyecto.
- Identificación de Necesidades de Modificación:
- Si el prototipo falló prematuramente o mostró un modo de falla indeseable (ej. frágil en lugar de dúctil), es necesario identificar la causa raíz y proponer modificaciones para corregir la debilidad (ej. reforzar una sección, cambiar un detalle de conexión, añadir rigidizadores).
- Si el prototipo mostró una rigidez significativamente menor a la esperada, pueden requerirse cambios para aumentar la inercia de la sección o mejorar la rigidez de las conexiones.
- Si el prototipo demostró una sobrerresistencia o sobrerrigidez considerable respecto a los requisitos, podría explorarse una optimización del diseño para reducir peso y coste, siempre manteniendo los márgenes de seguridad adecuados.
- Si el ensayo reveló problemas de montaje o funcionales, se deben proponer cambios en los detalles constructivos o en los componentes asociados.
- Propuesta de Modificaciones de Diseño: Los ingenieros de diseño elaboran propuestas concretas de cambio, basadas en los hallazgos y en su experiencia. Estas propuestas pueden ir desde ajustes menores en dimensiones o detalles de soldadura hasta rediseños más sustanciales de secciones o conexiones.
- Re-análisis del Diseño Modificado: Las modificaciones propuestas se incorporan en los modelos de cálculo (FEA) o en los análisis manuales. Se vuelve a verificar que el diseño modificado cumple con todos los requisitos de resistencia, rigidez, estabilidad y funcionalidad, ahora con mayor confianza gracias a la calibración implícita o explícita del modelo con los datos del ensayo.
- Evaluación de Impacto: Analizar el impacto de las modificaciones en otros aspectos del proyecto: coste de fabricación, programa de ejecución, interacción con otros elementos estructurales o sistemas.
- Documentación Formal de Cambios: Registrar formalmente los cambios realizados en los planos, especificaciones técnicas y memoria de cálculo, indicando claramente la justificación basada en los resultados del prototipo/ensayo. Mantener la trazabilidad del diseño es fundamental.
- Comunicación y Aprobación: Comunicar los cambios y su justificación al cliente y a las demás partes relevantes (arquitecto, constructor, interventoría). En algunos casos, los cambios pueden requerir una aprobación formal.
- Actualización de Planes de Fabricación e Inspección: Asegurar que los planos y procedimientos de fabricación reflejen el diseño final modificado y que los planes de inspección y control de calidad se ajusten si es necesario.
Este ciclo de retroalimentación (Diseño -> Prototipo/Ensayo -> Análisis -> Modificación -> Re-análisis -> Diseño Final) es lo que verdaderamente aporta valor a la fase de prototipado. Convierte la incertidumbre inicial en conocimiento aplicado, resultando en un diseño final más robusto, fiable y optimizado.
Presentación al Cliente: Beneficios y Confianza Ganada
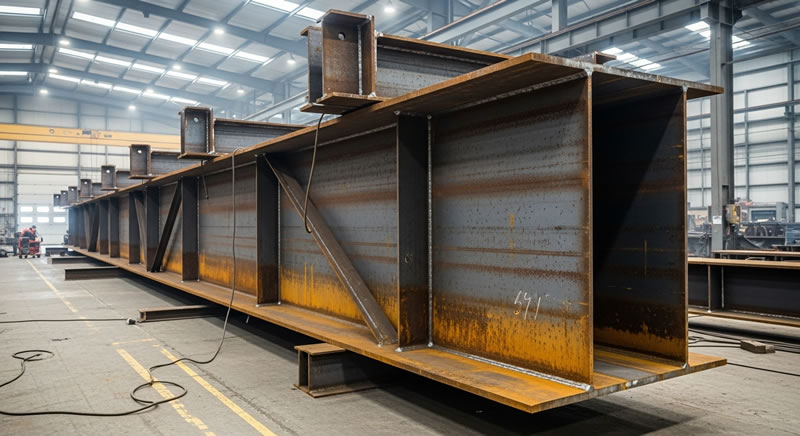
Comunicar eficazmente al cliente los resultados y, sobre todo, los beneficios derivados de la realización de prototipos y ensayos específicos es crucial. A menudo, esta fase representa una inversión adicional de tiempo y dinero para el cliente, por lo que es fundamental demostrar el valor obtenido y la confianza ganada en la solución final.
La presentación al cliente debe enfocarse en:
- Transparencia del Proceso: Explicar claramente por qué se recomendó la fase de prototipado (complejidad, criticidad, innovación), cómo se diseñó el prototipo para ser representativo y cómo se ejecutó el ensayo siguiendo un protocolo riguroso.
- Presentación Clara de Resultados: Mostrar los resultados clave del ensayo de forma comprensible, utilizando gráficos (curvas carga-desplazamiento), fotografías y vídeos. Comparar los resultados experimentales con las predicciones iniciales del diseño.
- Énfasis en la Validación y Verificación:
- Si el ensayo confirmó las predicciones del diseño, resaltar que esto valida las hipótesis de cálculo y proporciona una alta confianza en que la viga real se comportará según lo esperado. Se ha verificado experimentalmente el desempeño.
- Si el ensayo reveló discrepancias o requirió modificaciones en el diseño, explicar cómo esta información fue vital para identificar y corregir una potencial debilidad o comportamiento no deseado ANTES de la fabricación o instalación final. Demostrar cómo el proceso llevó a un diseño final mejorado y más seguro.
- Cuantificación de Beneficios:
- Mayor Seguridad y Fiabilidad: El beneficio más importante. El ensayo proporciona evidencia física del desempeño estructural, reduciendo incertidumbres y aumentando la confianza en la seguridad a largo plazo de la estructura, especialmente relevante para proyectos críticos o en zonas de riesgo como las sísmicas de Colombia.
- Mitigación de Riesgos: Demostrar cómo el ensayo ayudó a mitigar riesgos técnicos (falla estructural, desempeño inadecuado) y, potencialmente, riesgos económicos asociados a reparaciones costosas, retrasos en obra o fallos en servicio.
- Optimización del Diseño: Si el ensayo permitió optimizar el diseño (reduciendo peso/coste sin comprometer seguridad), cuantificar este beneficio.
- Validación de Innovación: Si se trataba de un diseño innovador, el ensayo proporciona la validación necesaria para implementar la nueva solución con confianza.
- Cumplimiento Regulatorio y Aseguramiento de Calidad: El ensayo puede ser un requisito o una fuerte evidencia para demostrar el cumplimiento de normativas exigentes o para satisfacer los requisitos de aseguradoras o entidades de control.
- Generación de Confianza: El hecho de haber realizado un proceso de validación tan riguroso demuestra el compromiso del equipo de diseño y fabricación con la calidad, la seguridad y la excelencia técnica. Esto fortalece la relación de confianza con el cliente.
- Documentación Completa: Entregar al cliente un informe detallado del ensayo, incluyendo el protocolo, la descripción del montaje, la instrumentación, los resultados brutos y procesados, el análisis, la correlación con modelos, las conclusiones y la documentación visual.
La inversión en prototipos y ensayos se justifica plenamente cuando se comunica como una medida proactiva para garantizar el éxito del proyecto, la seguridad de la estructura y la tranquilidad del cliente. Es una demostración tangible de ingeniería de alto nivel aplicada a soluciones personalizadas.
Finalmente, se resumen los beneficios clave comunicados al cliente:
Beneficio Directo para el Cliente | Descripción | Impacto en el Proyecto |
---|---|---|
Mayor Seguridad Estructural Confirmada | Evidencia física del comportamiento real bajo carga, validando márgenes de seguridad. | Reducción del riesgo de falla, cumplimiento normativo, tranquilidad a largo plazo. Protección de vidas y activos. |
Fiabilidad del Desempeño Asegurada | Confirmación experimental de la rigidez, ductilidad y modos de falla esperados. | Funcionamiento adecuado de la estructura bajo cargas de servicio y extremas (sismo, viento). |
Mitigación Proactiva de Riesgos Técnicos | Identificación y corrección temprana de posibles debilidades o comportamientos no previstos. | Prevención de costosos problemas durante la construcción o la vida útil de la estructura. |
Validación de Diseños Innovadores | Confirmación de la viabilidad y seguridad de soluciones no estándar o sin precedentes. | Permite la implementación de diseños optimizados o arquitectónicamente complejos con confianza. |
Optimización Potencial de Costos | Posibilidad de refinar el diseño basado en el desempeño real, eliminando conservadurismos innecesarios. | Reducción del peso del acero, simplificación de detalles, ahorro en materiales y fabricación (si aplica). |
Confianza Reforzada en la Solución | Demostración de rigor técnico y compromiso con la calidad por parte del equipo de diseño/fabricación. | Mayor tranquilidad para el cliente, facilitación de aprobaciones, mejora de la reputación del proyecto. |
Prevención de Problemas de Montaje/Funcionales | Identificación y solución de problemas de ensamblaje o interacción con otros sistemas (si se hicieron ensayos funcionales). | Reducción de retrasos y sobrecostos durante la fase de construcción. |